Niniejsza instrukcja obsługi ma służyć jako przewodnik podczas obsługi prasy RFlex . Aby zapewnić optymalną wydajność zgrzewarki, prosimy dokładnie przestrzegać zaleceń i specyfikacji.
Spis treści
- Rozdział 1: Przeznaczenie
- Rozdział 2: Znaki bezpieczeństwa i piktogramy
- Rozdział 3: Dane techniczne
- Rozdział 4: Opis techniczny
- Rozdział 5: Montaż i instalacja
- Rozdział 6: Obsługa
- Rozdział 7: Wybór parametrów spoiny
- Rozdział 8: Konserwacja
- Rozdział 9:
Bezpieczeństwo i higiena pracy
- Rozdział 10: Dokumentacja elektryczna
- Rozdział 11: Dokumentacja pneumatyczna
- Rozdział 12: Instrukcje ogólne
- Rozdział 13: Załączniki
- Rozdział 14: Dodatkowe dokumenty maszyny
Aby uzyskać więcej informacji technicznych dotyczących tego urządzenia, proszę zadzwonić do naszego Centrum Rozwiązywania Problemów pod numer 1-855-888-WELD lub wysłać wiadomość e-mail na adres service@weldmaster.com.
1. 0 Przegląd urządzenia / Przeznaczenie
Prasa RFlex jest najmniejszą maszyną w naszej linii maszyn częstotliwości radiowej. Jest solidnie skonstruowana i zaprojektowana z myślą o dokładności i długiej żywotności oraz posiada bardzo wytrzymały suwak montażowy z głowicą stalową, uformowany z podwójnym mechanizmem "V".
Do prac związanych ze "zszywaniem" zaleca się stosowanie małego uchwytu narzędziowego, zapewniającego dobrą widoczność i dostęp do obszaru roboczego. Do innych zastosowań można dostarczyć duże mocowanie zapewniające sztywne podparcie na szerokim obszarze narzędzia. Dostępne są również rozwiązania zwiększające przestrzeń gardzieli, w przypadku gdy nadmiar materiałów musi być umieszczony za oprzyrządowaniem.
Maszyna jest szeroko stosowana w przemyśle medycznym, motoryzacyjnym i odzieżowym do zgrzewania małych, dodatkowych części, takich jak rurki, zawory powietrza i płynów, haczyki, przelotki, płyty itp. RFlex Prasa ma moc wyjściową HF od 0,5 do 4 kW. Maszyna jest idealnym narzędziem do produkcji pomocniczej, gdzie precyzja, łatwość obsługi ręcznej, trwałość i wytrzymałość są kluczowe. Miller Weldmaster zawsze stawia na pierwszym miejscu jakość, precyzję, wydajność, bezpieczeństwo i prostotę konstrukcji.
NAJWAŻNIEJSZE CECHY MASZYNY:
- rutynowa konserwacja maszyny jest bardzo prosta;
- Nacisk można precyzyjnie wyregulować;
- producent zainstalował przycisk awaryjny na panelu sterowania;
- Maszyna jest wyposażona w kolumnę świateł sygnalizacyjnych, aby zwiększyć bezpieczeństwo operatora, gdy maszyna jest włączona;
- Operator może programować i kontrolować cykl pracy maszyny dzięki dotykowemu panelowi HMI;
- Narzędzie do programowania umożliwia operatorowi wprowadzenie do systemu takich parametrów jak: czas i moc spawania wraz z czasem chłodzenia;
- Za pomocą panelu HMI zainstalowanego na maszynie operator może zapisać wiele programów spawania dla różnych rodzajów materiałów, nie mówiąc już o tych używanych do pracy z różnymi rodzajami elektrod;
- urządzenie jest wyposażone w dodatkową elektrodę uziemiającą, aby chronić użytkownika przed zwiększonym poziomem promieniowania niejonizującego HF emitowanego przez urządzenie;
- ZTG HF AutoTuning System™ - maszyna jest wyposażona w automatyczny system kontroli mocy wyjściowej w celu zwiększenia bezpieczeństwa operatora;
- ZTG SafeDOWN™ - maszyna jest wyposażona w system, który powinien skutecznie chronić operatora przed elektrodą podczas jej opuszczania;
- ZTG Flash™ - kolejny system maszyny, który ma za zadanie chronić elektrodę i spawany surowiec przed ewentualnymi uszkodzeniami spowodowanymi zajarzeniem łuku;
- Wszystkie maszyny otrzymały certyfikaty zgodności CE
TECHNOLOGIA WYSOKIEJ CZĘSTOTLIWOŚCI:
Spawanie wysokoczęstotliwościowe, znane jako spawanie częstotliwością radiową (RF) lub spawanie dielektryczne, to proces łączenia materiałów poprzez zastosowanie energii o częstotliwości radiowej do łączonego obszaru. Powstała spoina może być tak mocna, jak oryginalne materiały.
Spawanie HF opiera się na pewnych właściwościach spawanego materiału, które powodują wytwarzanie ciepła w szybko zmieniającym się polu elektrycznym. Oznacza to, że tylko niektóre materiały mogą być spawane przy użyciu tej techniki. Proces ten polega na poddaniu łączonych części działaniu pola elektromagnetycznego o wysokiej częstotliwości (najczęściej 27,12 MHz), które jest zwykle stosowane między dwoma metalowymi prętami. Pręty te działają również jako aplikatory ciśnienia podczas ogrzewania i chłodzenia. Dynamiczne pole elektryczne powoduje oscylację cząsteczek w polarnych tworzywach termoplastycznych. W zależności od ich geometrii i momentu dipolowego, cząsteczki te mogą przekładać część tego ruchu oscylacyjnego na energię cieplną i powodować nagrzewanie materiału. Miarą tej interakcji jest współczynnik strat, który zależy od temperatury i częstotliwości.
Polichlorek winylu (PVC) i poliuretany to najpopularniejsze tworzywa termoplastyczne zgrzewane w procesie RF. Możliwe jest spawanie RF innych polimerów, w tym nylonu, PET, PET-G, A-PET, EVA i niektórych żywic ABS, ale wymagane są specjalne warunki, na przykład nylon i PET można spawać, jeśli oprócz mocy RF stosowane są wstępnie podgrzane pręty spawalnicze.
Spawanie HF generalnie nie jest odpowiednie dla PTFE, poliwęglanu, polistyrenu, polietylenu lub polipropylenu. Jednak ze względu na zbliżające się ograniczenia w stosowaniu PVC, opracowano specjalny gatunek poliolefiny, który może być zgrzewany RF.
Podstawową funkcją zgrzewania HF jest utworzenie złącza w dwóch lub więcej grubościach materiału arkuszowego. Istnieje szereg opcjonalnych funkcji. Narzędzie spawalnicze może być grawerowane lub profilowane, aby nadać całemu spawanemu obszarowi dekoracyjny wygląd lub może zawierać technikę wytłaczania w celu umieszczenia napisów, logo lub efektów dekoracyjnych na spawanych elementach. Dzięki zastosowaniu krawędzi tnącej przylegającej do powierzchni spawania, proces może jednocześnie spawać i ciąć materiał. Krawędź tnąca ściska gorące tworzywo sztuczne wystarczająco, aby umożliwić oderwanie nadmiaru złomu, stąd proces ten jest często określany jako zgrzewanie z rozerwaniem.
UWAGA: Producent nie ponosi odpowiedzialności za jakiekolwiek szkody lub obrażenia powstałe w wyniku niewłaściwego użytkowania tego urządzenia.
UWAGA: Aby korzystać z urządzenia w optymalny i bezpieczny sposób, proszę uważnie przeczytać i przestrzegać wszystkich instrukcji zawartych w niniejszej instrukcji obsługi i konserwacji.
UWAGA: Wszyscy pracownicy, przeszkoleni w zakresie bezpieczeństwa pracy, procedur operacyjnych i ryzyka związanego ze spawarką, a także osoby wykwalifikowane do obsługi spawarki, proszeni są przez Wykonawcę o złożenie czytelnego podpisu na załączonym formularzu.
UWAGA: Zgrzewarka wysokiej częstotliwości została zaprojektowana i wyprodukowana w wersji nieodpowiedniej dla osób niepełnosprawnych. Jeśli maszyna ma być obsługiwana przez osoby niepełnosprawne, należy ją odpowiednio dostosować po konsultacji z producentem.
2.0 Znaki bezpieczeństwa i piktogramy
2.1 Informacje ogólne
Aby używać spawarki w optymalny i bezpieczny sposób, proszę uważnie przeczytać i przestrzegać wszystkich instrukcji zawartych w niniejszej instrukcji obsługi i konserwacji, a w szczególności wszystkich ostrzeżeń, zakazów, ograniczeń i nakazów oraz znaków.
Na podstawie informacji zawartych w niniejszej Instrukcji obsługi i konserwacji Klient musi opracować Instrukcje stanowiskowe dla pracowników.
Klient ponosi pełną, prawną i materialną odpowiedzialność za wszelkie zdarzenia wynikające z niewystarczającej znajomości niniejszej Instrukcji Obsługi i Konserwacji lub nieprzestrzegania zasad Bezpieczeństwa i Higieny Pracy.

UWAGA: Przed przystąpieniem do jakiejkolwiek pracy jakiejkolwiek osoby obsługującej zgrzewarkę HF należy obowiązkowo zapoznać się z Instrukcją Obsługi i Konserwacji.
UWAGA: Każdy odbiorca lub osoba przez niego upoważniona na podstawie niniejszej Instrukcji Obsługi i Konserwacji oraz właściwej charakterystyki technologii produkcji ma prawo do korzystania z urządzenia w sposób zgodny z jego przeznaczeniem. należność obowiązkowa wydać PODRĘCZNIK STANOWISKA PRACY dla operatorów.
UWAGA: Zgrzewarka wysokiej częstotliwości może być obsługiwana WYŁĄCZNIE przez pracowników, którzy zostali przeszkoleni w zakresie obsługi urządzenia i BEZPIECZEŃSTWA PRZEMYSŁOWEGO, ze szczególnym uwzględnieniem możliwego ryzyka związanego z urządzeniem.
UWAGA: Przez cały okres eksploatacji urządzenia Producent sugeruje Nabywcy korzystanie z usług przeszkolonego personelu serwisowego zapewnionego przez Producenta lub autoryzowanych przez Producenta zespołów serwisowych.
UWAGA: Producent zdecydowanie zaleca instalowanie spawarki wyłącznie w środowisku przemysłowym.
UWAGA: Maszyna musi być odpowiednio wypoziomowana i musi mieć stałe miejsce pracy.
UWAGA: Nieostrożne obchodzenie się z maszyną podczas transportu (przenoszenia) może spowodować poważne obrażenia lub wypadki.
UWAGA: Generator jest zasilany niebezpiecznym dla życia napięciem sieci energetycznej 3 x220 VAC; 50 Hz. Urządzenie ma wysokie napięcie do 5000 VDC. Wszelkie czynności serwisowe lub zapobiegawcze mogą być wykonywane wyłącznie przez przeszkolony personel z uprawnieniami wymaganymi przez prawo.
UWAGA: Nabywca powinien koniecznie zadbać o prawidłowe wykonanie i regularną kontrolę prewencyjną instalacji ochrony przeciwporażeniowej dla każdego używanego urządzenia. Wszelka odpowiedzialność w tym zakresie spoczywa na Nabywcy.
UWAGA: Napięcie lampy musi być takie samo, jak podane w karcie katalogowej produktu - można je regulować za pomocą rozgałęzień po stronie pierwotnej transformatora żarowego.
UWAGA: Lampa musi być podgrzewana przez około godzinę po instalacji.
UWAGA: Wszelkie prace w strefie aktywnej jednostki prasującej prasy, tj. wymiana urządzenia, mogą być wykonywane ze szczególną ostrożnością wyłącznie przez przeszkolony zespół serwisowy.
UWAGA: Awaryjne zatrzymanie maszyny jest możliwe w dowolnym momencie poprzez naciśnięcie przycisku EMERGENCY Przycisk STOP (czerwony przycisk na żółtym tle).
UWAGA: Środowisko pracy maszyny, podłoga oraz ręczne uchwyty i uchwyty muszą być zawsze czyste i wolne od wszelkich zanieczyszczeń, smaru lub błota, aby zmniejszyć ryzyko poślizgnięcia się lub upadku do minimalnego możliwego poziomu.
PRZESTROGA: Przed zdjęciem paneli dostępu lub otwarciem drzwi należy odłączyć urządzenie od zasilania. Wszystkie osłony i panele dostępu muszą znajdować się na swoim miejscu przed przystąpieniem do obsługi urządzenia.
UWAGA: Temperatura elektrody wynosi do 100 °C. Dlatego dotknięcie elektrody może spowodować poparzenie.
UWAGA: Lampa zawiera metale ziem rzadkich i tlenki metali ziem rzadkich, które są wysoce toksyczne. W przypadku stłuczenia, lampę należy zutylizować z zachowaniem najwyższej ostrożności i przy pomocy wyspecjalizowany usługi.
UWAGA: Zgrzewarka wysokiej częstotliwości jest źródłem niejonowego promieniowania elektromagnetycznego. Po zainstalowaniu urządzenia u nabywcy należy wykonać pomiary promieniowania niejonowego. Pomiary promieniowania powinny być wykonywane przez autoryzowaną firmę.
UWAGA: Zgrzewarki wysokiej częstotliwości muszą pracować w stabilnym miejscu pracy, ponieważ transpozycja wymaga nowych pomiarów natężenia promieniowania niejonowego..
UWAGA: Osobom z wszczepionym rozrusznikiem serca nie wolno przebywać w strefie aktywnego promieniowania..
UWAGA: Producent sugeruje, aby nie zatrudniać kobiet w ciąży lub karmiących piersią w strefie aktywnego promieniowania niejonowego..
UWAGA: Zgrzewarka wysokiej częstotliwości została zaprojektowana i wyprodukowana w wersji nieodpowiedniej dla osób niepełnosprawnych. Jeśli maszyna ma być obsługiwana przez osoby niepełnosprawne, należy ją odpowiednio dostosować po konsultacji z producentem.


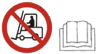

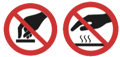



























3.0 Dane techniczne
Typ maszynytyp |
ZD-NX-4 |
Materiały spawalnicze |
PVC, tkaniny powlekane PVC |
Zasilanie |
3 x 220 V; 50/60Hz |
Moc wyjściowa HF |
4 kW |
Sterownik PLC |
Delta |
Napięcie sterujące |
24 VDC |
Moc zainstalowana |
6 kVA |
Regulacja wydajności wyjściowej |
ręczny/autotuner |
Główne wycięcie |
D25 A; opóźniony |
Częstotliwość pracy |
27,12 MHz |
Stabilność częstotliwości |
+/- 0.6 % |
System przeciwbryzgowy, ZEMAT TG |
Bardzo czuły czujnik ARC |
Zużycie sprężonego powietrza |
11 nl/cykl |
Rozmiar stołu roboczego |
800 x 410 mm |
Powierzchnia spawania |
100mm^2 |
Skok siłownika |
~ 100 mm |
Napęd elektrody dociskowej |
pneumatyczny |
Napęd elektrody uziemiającej |
pneumatyczny |
Siła nacisku (maks.) |
1200 kG |
Lampa generatora |
ITL 12-1 |
Płyn chłodzący |
powietrze |
Waga maszyny |
~ 3500 kg |
Wymiary |
PROSZĘ ZOBACZYĆ DODATKI |
4.0 Opis techniczny
Głównym elementem zgrzewarki wysokiej częstotliwości ZD-NX-4 jest konstrukcja nośna wykonana ze spawanych blach i profili stalowych. Wszystkie pozostałe części maszyny są zamontowane na wspomnianej konstrukcji. Konstrukcję nośną można podzielić na dwie podstawowe części:
- Z tyłu znajduje się generator wysokiej częstotliwości wraz z transformatorem anodowym i skrzynką przełączników. Ta część jest zamknięta w zdejmowanych osłonach chronionych przez klucz wyłącznika krańcowego.
- z przodu znajduje się stół roboczy, na którym układany jest spawany materiał. Spawanie jest wykonywane, gdy elektroda jest dociskana do stołu przez izolowany zacisk połączony z dźwignią nożną za pomocą płyty pośredniej. Nad stołem znajduje się panel sterowania HMI
Zastosowane osłony wraz z przełącznikami mają za zadanie zminimalizować emisję promieniowania niejonizującego. Obsługa spawarki bez założonych osłon jest surowo ZABRONIONA!!!
- SYSTEM STEROWANIA składający się ze sterownika PLC i panelu dotykowego HMI, elementów sterujących i obsługowych umieszczonych na głównym panelu sterowania oraz innych urządzeń elektrycznych i elektronicznych umieszczonych na maszynie.
- SPRĘŻONE POWIETRZE składa się między innymi z zespołu przygotowania sprężonego powietrza, zaworów przełączających i siłowników pneumatycznych.
- Układ GENERUJĄCY składający się z samowzbudnego generatora wysokiej częstotliwości o stałych rozpadu, który składa się głównie z obwodu LC o wysokim współczynniku Q ustawionym na 27,30 MHz. System składa się również z lampy o fali bieżącej, transformatora anodowego, transformatora żarnika i układu chłodzenia lampy;
Zastosowane osłony wraz z przełącznikami mają za zadanie zminimalizować emisję promieniowania niejonizującego. Obsługa spawarki bez założonych osłon jest surowo ZABRONIONA!!!
Maszyna w pełni wykorzystuje następujące systemy:
- JEDNOSTKA STERUJĄCA składająca się ze sterownika PLC z panelem dotykowym HMI, elementów sterujących i wskaźników umieszczonych na głównym panelu sterowania przymocowanym do wysięgnika oraz innych urządzeń elektrycznych i elektronicznych zainstalowanych na tej maszynie; oraz
- ZESTAW SPRĘŻONEGO POWIETRZA składający się głównie z zestawu przygotowania sprężonego powietrza, w tym: zaworów rozdzielczych i siłowników pneumatycznych; oraz
- UKŁAD GENERUJĄCY składający się z samowzbudnego generatora wysokiej częstotliwości o stałych rozpadu, który składa się głównie z obwodu LC o wysokim współczynniku Q ustawionym na 27,30 MHz. System składa się również z lampy o fali bieżącej, transformatora anodowego, transformatora żarnika i układu chłodzenia lampy;
Uchwyt elektrody spawalniczej jest wyposażony w automatyczny system uchwytu sterowany z panelu dotykowego HMI. Pozwala on na beznarzędziową wymianę elektrod.
Zastosowane osłony wraz z przełącznikami mają za zadanie zminimalizować emisję promieniowania niejonizującego. Obsługa spawarki bez założonych osłon jest surowo ZABRONIONA!!!
Dodatkowo na podwoziu maszyny zainstalowano wskaźniki laserowe, które ułatwiają pozycjonowanie spawanego materiału na stole roboczym.
5.0 Montaż i instalacja
5. 1 Informacje i znaki dotyczące ograniczeń i nakazów
Producent zapewnia odpowiednie opakowanie urządzenia na czas transportu. Rodzaj i trwałość opakowania są dostosowane do odległości i środka transportu, a co za tym idzie do potencjalnego ryzyka uszkodzeń podczas transportu. Producent sugeruje, aby każdy Klient korzystał ze środków transportu i serwisu technicznego Producenta.
Przechowywanie urządzenia nie wiąże się z żadnymi szczególnymi wymaganiami, poza odpowiednim środowiskiem przechowywania.
Pomieszczenie magazynowe musi zapewniać wystarczającą ochronę przed czynnikami atmosferycznymi, powinno być możliwie suche i mieć dopuszczalny poziom wilgotności (poniżej 70%). Konieczne jest również zapewnienie odpowiedniej ochrony przed korozją, szczególnie w przypadku elementów metalowych, które nie są malowane ze względów technicznych.
Jeśli urządzenie jest dostarczane w pudełku i jest owinięte plastikiem wytwarzającym atmosferę antykorozyjną, urządzenie powinno pozostać owinięte i zapakowane przez cały okres przechowywania.
W celu ochrony przed wilgocią zaleca się, aby urządzenie nie było przechowywane bezpośrednio na podłodze pomieszczenia magazynowego, ale raczej na paletach.
Elementem, który wymaga szczególnej uwagi i obsługi na każdym etapie - w tym przechowywania - jest lampa generatora (trioda). Lampa musi być przechowywana w oryginalnym opakowaniu, w pozycji pionowej, z anodą skierowaną do góry lub do dołu, w suchym pomieszczeniu. Lampa jest metalowo-ceramicznym elementem pracującym w warunkach wysokiej próżni, który jest niezwykle delikatny i nie może zostać uderzony lub upuszczony nawet z niewielkiej wysokości.
Uderzanie, upuszczanie, potrząsanie lub przechylanie lampy przez dłuższy czas może spowodować trwałe i nieodwracalne uszkodzenie lampy. W szczególności, żarnik katody lampy może zostać uszkodzony, co w najbardziej ekstremalnych przypadkach może prowadzić do wewnętrznych zwarć lub pęknięcia lampy.
UWAGA: Lampa zawiera metale ziem rzadkich i tlenki metali ziem rzadkich, które są wysoce toksyczne. W przypadku stłuczenia lampę należy zutylizować z zachowaniem najwyższej ostrożności i przy pomocy wyspecjalizowanych służb.
Powyższe postanowienia mają na celu poinstruowanie i ostrzeżenie wszystkich osób i służb, które mogą mieć kontakt z tym urządzeniem, o jego wysokiej podatności na wszelkie impulsy i udary. Jednocześnie w toku postępowania reklamacyjnego nie będą uwzględniane żadne roszczenia związane z opisanymi powyżej trwałymi uszkodzeniami.
Należy również podkreślić, że lampa generatora jest bardzo drogim komponentem.
W przypadku jakichkolwiek wątpliwości zaleca się konsultację z wyspecjalizowanym personelem Producenta.
5.2 Transport urządzenia
Podmiot odpowiedzialny za transport i instalację maszyny w Zakładzie Zamawiającego powinien zostać ustalony na etapie podpisywania umowy i nie później niż po przeprowadzeniu końcowego testu akceptacyjnego maszyny w Zakładzie Producenta, przed przekazaniem urządzenia Zamawiającemu.
UWAGA: Nieostrożne obchodzenie się z urządzeniem podczas transportu/przenoszenia może spowodować poważne obrażenia lub wypadki.
ZABRANIA SIĘ montażu, demontażu lub transportu maszyny przez personel bez odpowiednich kwalifikacji lub bez zapoznania się z wymogami bezpieczeństwa opisanymi w niniejszej Instrukcji obsługi i konserwacji. Takie działania mogą spowodować wypadki lub szkody materialne.
Mając na uwadze specyfikę urządzenia, Producent sugeruje, aby każdy Zamawiający korzystał ze środków transportu i serwisu technicznego Producenta.
Lampa zasilająca musi zostać zdemontowana przed jakimkolwiek transportem lub przenoszeniem.
Lampa musi być zawsze transportowana lub przenoszona w oryginalnym opakowaniu producenta, w pozycji pionowej, z anodą skierowaną do góry lub do dołu, bez uderzania lub potrząsania lampą.
UWAGA: Maszyna powinna być transportowana w pozycji pionowej.
Ze względu na swoje rozmiary i konstrukcję, urządzenie wymaga demontażu i odłączenia niektórych komponentów i jednostek na czas transportu lub przeprowadzki. Konieczny jest demontaż delikatnych i drogich komponentów i narzędzi (które powinny być transportowane w oddzielnej walizce). Bezwzględnie konieczny jest demontaż lampy generatora.
Maszyna powinna być przemieszczana za pomocą urządzeń dźwigowych - dźwigów, wózków widłowych, wózków paletowych - o odpowiednim udźwigu umożliwiającym bezpieczny transport generatora, a osoby obsługujące takie urządzenia dźwigowe powinny posiadać wszelkie wymagane prawem uprawnienia i kwalifikacje.
Wszystkie komponenty urządzenia, które mogą zostać uszkodzone podczas transportu (jeśli nie zostanie użyte opakowanie o wysokiej wytrzymałości) lub przez urządzenia podnoszące lub przenoszące, powinny być odpowiednio zabezpieczone (pod warunkiem, że zostały zdemontowane i zapakowane oddzielnie).
Aby zapewnić stabilną pozycję urządzenia, bardzo ważne jest zapewnienie odpowiedniego zabezpieczenia maszyny na czas długiego transportu (pasy bezpieczeństwa, śruby kotwiące), a także ochrony i pomocy podczas transportu na miejscu.
Jeśli maszyna nie jest wyposażona w odpowiednie mocowania, możliwe jest użycie innych dostępnych otworów lub elementów o wystarczającej wytrzymałości, aby zapewnić odpowiednie wyważenie i stabilizację generatora i innych części maszyny.
Waga maszyny (około 350 kg) musi być zdecydowanie wzięta pod uwagę podczas planowania transportu.
5.3 Instalacja w miejscu eksploatacji
W zależności od stopnia skomplikowania maszyny, instalację w miejscu eksploatacji powinien przeprowadzić personel Zamawiającego, po zapoznaniu się z niniejszą Instrukcją Obsługi i Konserwacji lub pracownicy serwisu technicznego Producenta, we współpracy z personelem Zamawiającego.
Proszę pamiętać, że odpowiednie ustawienie i instalacja zgrzewarki ma kluczowe znaczenie dla zapewnienia jej optymalnego funkcjonowania, a także komfortu i bezpieczeństwa operatora w otoczeniu urządzenia.
Zamawiający jest odpowiedzialny za przygotowanie miejsca do instalacji urządzenia, dostępność i przygotowanie przyłączy elektrycznych oraz realizację poszczególnych wymagań projektu technicznego i technicznych testów odbiorczych dopuszczających cały generator do użytku.
Producent przekaże Zamawiającemu wszelkie wymagane instrukcje i informacje w tym zakresie.
UWAGA: Proszę upewnić się, że podłoga/powierzchnia/fundamenty, na których ma zostać ustawiona maszyna, mają wystarczającą wytrzymałość, biorąc pod uwagę ciężar, powierzchnię i rozkład ciężaru maszyny na jej punkty podparcia (zazwyczaj nogi).
UWAGA: Urządzenie musi być odpowiednio wypoziomowane i musi mieć stałe miejsce pracy.
Optymalnym miejscem pracy zgrzewarki HF jest powierzchnia betonu nie pokryta lub pokryta bardzo cienką warstwą materiału nieprzewodzącego.
Powierzchnia powinna być wykonana zgodnie z konkretnym projektem, zgodnie z normami konstrukcyjnymi i bezpieczeństwa, a także zgodnie z wymaganiami dotyczącymi pozycji równoległych, prostopadłych i płaskich.
UWAGA: Zamawiający ponosi wyłączną odpowiedzialność za realizację powyższych warunków.
Po umieszczeniu spawarki w wybranym miejscu, należy ją wypoziomować, sprawdzić jej stan techniczny i usunąć wszelkie usterki, które mogły powstać podczas transportu. Następnie należy rozpakować, ustawić, wypoziomować i zamocować generator. Lampa generatora wysokiej częstotliwości powinna zostać zamontowana na samym końcu procesu instalacji. Zadanie to należy wykonać ze szczególną uwagą, zarówno podczas montażu lampy w gnieździe/podstawie, jak i podczas podłączania styków elektrycznych lampy. Proszę podłączyć złącza konsoli sterującej do odpowiednio oznaczonych gniazd na prasie. Zaleca się, aby instalacja maszyny po transporcie odbywała się pod bezpośrednim nadzorem przedstawiciela producenta.
UWAGA: Jeśli wyżej wymienione zadania są wykonywane przez przedstawiciela Klienta, powinny być one wykonywane ściśle zgodnie z opisem zawartym w niniejszej Instrukcji Obsługi i Konserwacji i/lub instrukcjami dostarczonymi przez producenta podczas technicznego testu odbiorczego.
Spawarka może być używana wyłącznie w pomieszczeniach wolnych od pyłu, kwasów, siarki, oparów żrących i gazów łatwopalnych. Ze względu na generowane pole magnetyczne, w pobliżu spawarki nie należy umieszczać dużych metalowych przedmiotów. Maszyna może wpływać na działanie urządzeń elektronicznych (radio, telewizory, komputery) znajdujących się w pobliżu maszyny, w wyniku wysokiej czułości wejściowej wyżej wymienionych urządzeń. Optymalnym miejscem pracy urządzenia jest powierzchnia betonowa nie pokryta lub pokryta bardzo cienką warstwą materiału nieprzewodzącego.
5.4 Instalacja w miejscu eksploatacji
5.4.1 Instalacja w miejscu eksploatacji
UWAGA: Producent zdecydowanie zaleca instalowanie urządzenia wyłącznie w środowisku przemysłowym.
Maszyna będąca przedmiotem niniejszej instrukcji obsługi i konserwacji została zaprojektowana i wyprodukowana do pracy w środowisku przemysłowym w celu przetwarzania taśm przenośnikowych.
Specyficzne warunki pracy urządzeń, tj. wysoka wilgotność powietrza, wysoka temperatura, para wodna i zapylenie, zostały uwzględnione przez projektantów maszyny i nie wpływają na jej działanie, ale określają bardziej rygorystyczne wymagania dotyczące wykonywania programów prewencyjnych.
Maszyna nie może być używana w atmosferze zagrożonej wybuchem, w atmosferze silnie zapylonej, w środowisku o wysokiej wilgotności i/lub wysokiej temperaturze oraz w obecności agresywnych oparów (kwaśnych, zasadowych, organicznych lub nieorganicznych, mających potencjalnie lub faktycznie korozyjny wpływ).
Temperatura środowiska pracy powinna wynosić od +10º C do +40º C, a wilgotność względna: od 30% do 90%. Kondensacja wilgoci atmosferycznej lub jakichkolwiek agresywnych substancji na powierzchni urządzenia (lub któregokolwiek z jego elementów) jest niedopuszczalna.
Wymagane jest, aby długotrwała amplituda temperatury w ciągu dnia w pomieszczeniu pracy generatora nie przekraczała 10º C, a w przypadku wilgotności względnej: 10%.
Powyższa klauzula nie ma zastosowania do mediów lub substancji używanych do smarowania, konserwacji lub nieagresywnych substancji używanych w trakcie produkcji / eksploatacji urządzenia.
UWAGA: Jeśli występuje duża różnica między temperaturą zewnętrzną a temperaturą w pomieszczeniu, w którym zainstalowano urządzenie, urządzenie należy uruchomić po 24 godzinach od jego montażu w pomieszczeniu.
5.4.2 Oświetlenie
Wymagania dotyczące minimalnego natężenia oświetlenia stanowią, że na poziomej powierzchni roboczej natężenie oświetlenia, które można zaakceptować w pomieszczeniach, w których ludzie przebywają przez dłuższy czas, niezależnie od tego, czy wykonywane są jakiekolwiek czynności wzrokowe, powinno wynosić 300 lx.
W przypadku czynności wzrokowych, których poziom trudności jest wyższy niż przeciętny i gdy wymagany jest wysoki komfort widzenia, a także gdy większość operatorów ma ponad 40 lat, wymagane natężenie światła powinno być wyższe niż minimalne, tj. co najmniej 500 lx.
5.4.3 Hałas
Maszyna nie generuje hałasu na poziomie, który wymagałby użycia jakichkolwiek środków lub urządzeń ochrony personelu.
Należy jednak pamiętać, że wszystkie środowiska pracy charakteryzują się własną emisją hałasu, co może mieć wpływ na poziom hałasu emitowanego przez maszynę podczas jej pracy.
5.5 Parametry połączenia
5.5.1 Energia elektryczna
Podłączenie: 3 x 2200V; 50Hz (3P+N+PE), zabezpieczenie nadprądowe z opóźnieniem. Instalacja Klienta musi zapewniać środki ochrony przeciwporażeniowej zgodne z normą EN 60204-1:2018-12.
UWAGA: Po zamontowaniu lampy należy zawsze sprawdzić napięcie żarnika - patrz dane techniczne lampy.
5.5.2 Sprężone powietrze
Ciśnienie: 0,4 - 0,8 MPa, wymagana klasa czystości wg ISO8573-1 4-4-4, zużycie: 11 nl na jeden cykl.
UWAGA: Jeśli ciśnienie w układzie użytkownika końcowego jest wyższe niż 0,8 MPa, należy je zredukować do około 0,8 MPa za pomocą zaworu redukcyjnego zamontowanego na przyłączu spawarki.
5.6 Parametry połączenia
W zależności od złożoności systemu oraz kwalifikacji i uprawnień pracowników, podłączenie zgrzewarki w miejscu jej eksploatacji wykonują osoby wybrane przez Zamawiającego lub pracownicy serwisu technicznego Producenta, we współpracy z personelem Zamawiającego, za dodatkową opłatą lub nieodpłatnie, co jest każdorazowo uzgadniane przed przekazaniem zgrzewarki Zamawiającemu z zakładu Producenta.
Zawsze należy sprawdzić, czy wszystkie połączenia zostały wykonane zgodnie z dokumentacją urządzenia.
Należy zaznaczyć, że powyższe zadania wymagają odpowiednich kwalifikacji personelu, w tym stosownych uprawnień wydanych przez odpowiednie organy.
Dotyczy to zarówno specjalistycznych kwalifikacji, jak i ukończonych i ważnych szkoleń w zakresie bezpieczeństwa i higieny pracy, w tym w szczególności ryzyka związanego z tymi zadaniami.
6.0 Działanie
6.1 Przygotowanie maszyny do pracy - pierwsze uruchomienie
Procedura kontroli przed operacją:
- kontrolować i sprawdzać skuteczność środków ochrony przed porażeniem prądem elektrycznym
- kontrola i sprawdzenie napięcia zasilania - wartość i poprawność podłączenia faz, jeśli dotyczy kierunek obrotów silnika
- proszę sprawdzić napięcie żarówki
- zdjąć osłony ochronne spawarki i sprawdzić, czy nie ma drobnych uszkodzeń (czy przewody nie są przerwane, czy połączenia gwintowe nie są poluzowane itp.)
- rozpakować, sprawdzić i zainstalować lampy generatora.
UWAGA: Aby korzystać z urządzenia w optymalny i bezpieczny sposób, proszę uważnie przeczytać i przestrzegać wszystkich instrukcji zawartych w niniejszej instrukcji obsługi i konserwacji.
ZABRANIA SIĘ wykonywania jakichkolwiek prac przy maszynie zgrzewającej przez osoby, które nie zostały wcześniej przeszkolone w zakresie obsługi maszyn wysokiej częstotliwości i przepisów bezpieczeństwa przemysłowego, ze szczególnym uwzględnieniem możliwego ryzyka związanego z maszyną.
Pod warunkiem spełnienia wszystkich wymagań instalacyjnych i wykonania zadań opisanych w punkcie 5, jesteśmy gotowi do pierwszego uruchomienia zgrzewarki w środowisku produkcyjnym zakładu Zamawiającego.
UWAGA: Pierwsze uruchomienie maszyny należy przeprowadzić w obecności i pod nadzorem przedstawicieli Producenta.
6.2 Wymagania eksploatacyjne - Ogólne instrukcje i wytyczne
Wszelkie regulacje i kalibracje wymagane dla prawidłowych parametrów pracy urządzenia zostały wykonane przez Producenta w trakcie montażu i wewnętrznych procedur testowych. Ogólna zgodność z umownymi wymaganiami technicznymi oraz poprawność działania urządzenia potwierdzana jest podczas odbioru technicznego odbywającego się w siedzibie Producenta, w obecności przedstawiciela Zamawiającego, z wykorzystaniem oryginalnych surowców dostarczonych przez Zamawiającego do testów.
UWAGA: Ze względu na specyficzne właściwości urządzeń emitujących energię o wysokiej częstotliwości, konieczne jest przeprowadzanie niektórych pomiarów w miejscu pracy urządzenia w siedzibie Zamawiającego. Z tego samego powodu bardzo ważne jest, aby urządzenie miało stałe miejsce pracy.
Przed rozpoczęciem użytkowania maszyny i jej pierwszym uruchomieniem Odbiorca jest bezwzględnie zobowiązany do przeszkolenia pracowników, którzy będą jej przyszłymi operatorami.
UWAGA: Spawarka może być obsługiwana WYŁĄCZNIE przez pracowników, którzy zostali przeszkoleni w zakresie serwisowania maszyny i BEZPIECZEŃSTWA PRZEMYSŁOWEGO, ze szczególnym uwzględnieniem możliwego ryzyka związanego z maszyną. Takie szkolenie powinno zostać potwierdzone odpowiednim dokumentem podpisanym przez przeszkoloną osobę.
Ponadto, ze względu na różne cykle pracy wykonywane przez nasze maszyny w różnych środowiskach przemysłowych, Odbiorca ma bezwzględny obowiązek stworzenia jasnej i przejrzystej INSTRUKCJI OBSŁUGI urządzenia, dostosowanej do jego własnych cykli produkcyjnych.
UWAGA: Nabywca lub osoba przez niego upoważniona jest zobowiązana do wydania INSTRUKCJI OBSŁUGI na podstawie niniejszej instrukcji obsługi i konserwacji oraz charakterystyki technologii produkcji.
Ze względu na specyficzne właściwości urządzeń emitujących energię o wysokiej częstotliwości, konieczne jest przeprowadzenie określonych pomiarów w miejscu pracy urządzenia w siedzibie Zamawiającego. Z tego samego powodu bardzo ważne jest, aby urządzenie miało stałe miejsce pracy.
UWAGA: Zgrzewarka wysokiej częstotliwości jest źródłem niejonowego promieniowania elektromagnetycznego. Po zainstalowaniu urządzenia u nabywcy należy wykonać pomiary promieniowania niejonowego. Pomiary promieniowania powinny być wykonane przez autoryzowaną firmę i wyznaczyć granice strefy niebezpiecznej.
UWAGA: Urządzenie musi mieć stałe miejsce pracy. Każda zmiana lokalizacji urządzenia wymaga przeprowadzenia odpowiednich specjalistycznych pomiarów i wyznaczenia stref oddziaływania niejonizującego pola elektromagnetycznego.
PRZED URUCHOMIENIEM JEST ABSOLUTNIE KONIECZNE DO KONTROLI:
- Skuteczność środków ochrony przed porażeniem prądem elektrycznym;
- Napięcie zasilania - wartość i poprawność podłączenia faz;
- Kierunek obrotów silnika (jeśli dotyczy);
- Napięcie żarówki;
UWAGA: Napięcie lampy musi być takie samo, jak podane w karcie katalogowej produktu - można je regulować za pomocą rozgałęzień po stronie pierwotnej transformatora żarowego.
UWAGA: Ze względu na specyfikę urządzenia należy zawsze ostrzegać i informować personel o wysokim napięciu zasilania anody lampy i potencjalnym ryzyku śmiertelnego porażenia prądem elektrycznym o napięciu do 5000 VDC.
UWAGA: Lampa musi być podgrzewana przez około godzinę po instalacji.
- Pozycja uchwytu względem podstawy stołu roboczego;
- Emisja pola elektromagnetycznego - po dostosowaniu parametrów spawania, podczas procesu spawania;
INSTALACJA LAMPY GENERATORA
- zdjąć boczną osłonę ochronną generatora wykonaną z perforowanej blachy metalowej
- usunąć plastikową rurkę kierującą strumień powietrza
- włożyć lampę do gniazda - lampę można włożyć do gniazda tylko w jeden sposób (proszę nie używać nadmiernej siły)
- zamontować plastikową rurę kierującą strumień powietrza
- założyć i przymocować zapinkę czujnika temperatury do anody
- proszę upewnić się, że wyłącznik krańcowy czujnika przewodu został podłączony
- przymocować arkusze zasilające kondensatora rozdzielającego i kondensatora tarczowego do górnej części anody
- proszę nie zmieniać kształtu ani położenia metalowych elementów wewnątrz komory generatora
- podłączyć system zasilania do sieci zasilającej, zapewniając odpowiednią jakość systemu ochrony przeciwporażeniowej
- Proszę włączyć obwód żarzenia i jednostkę sterującą, przełączając przełącznik MAIN SWITCH do pozycji I-ON. Lampka kontrolna SUPPLY powinna się zaświecić (w razie potrzeby proszę nacisnąć niebieski przycisk RESET na kasecie sterowniczej);
UWAGA: Wentylator chłodzący lampę włącza się po włączeniu obwodu żarzenia lampy generatora. Jeśli zespół wentylatora nie działa, proszę nie używać urządzenia do czasu usunięcia usterki zespołu wentylatora!!!
- proszę sprawdzić napięcie żarzenia lampy generatora. Musi ono mieścić się w zakresie wymaganym przez producenta triody. W razie potrzeby można je wyregulować, zmieniając gałęzie transformatora. Czynności te powinien wykonywać przedstawiciel Producenta urządzenia lub (na ryzyko Klienta) inna osoba posiadająca odpowiednie kwalifikacje, tj. posiadająca uprawnienia wydane przez odpowiednie Stowarzyszenie Elektryków (w Polsce SEP) oraz wiedzę na temat zagrożeń i ryzyka związanego z obsługą zgrzewarki wysokiej częstotliwości, w szczególności potencjalnego ryzyka porażenia prądem o napięciu do 5000 V. Nowa lampa powinna świecić przez około 0,5 h przed włączeniem obwodu anodowego
- sprawdzić działanie jednostki sterującej zgodnie z procedurą opisaną w punkcie 6.
- Po dostosowaniu parametrów spawania, podczas procesu spawania, proszę sprawdzić emisję pola elektromagnetycznego.
WAŻNE: Jeśli obwody wysokiego napięcia zostały przypadkowo podłączone, gdy anoda jest odłączona lub lampa generatora jest uszkodzona, kondensatory filtra wysokiego napięcia muszą zostać rozładowane poprzez zwarcie ich z obudową na bardzo krótki czas.
UWAGA: Wszystkie czynności podczas rozruchu i pomiarów, gdy poziom bezpieczeństwa jest niższy (otwarte ekrany ochronne, zablokowane przełączniki kluczykowe), muszą zajmować jak najmniej czasu, a pełny poziom bezpieczeństwa pracy maszyny musi być zapewniony tak szybko, jak to możliwe.
UWAGA: Wszystkie czynności kontrolno-pomiarowe należy wykonywać po sprawdzeniu, czy przełączniki do regulacji napięcia anodowego znajdują się w pozycji 0 - OFF (nie dotyczy pomiaru emisji pola elektromagnetycznego).
UWAGA: Wszystkie czynności kontrolno-pomiarowe muszą być wykonywane wyłącznie przez upoważniony personel.
ZAWSZE ZABRANIA SIĘ rozpoczynania procesu spawania, tj. włączania wysokiego napięcia lampy, które inicjuje napięcie wysokiej częstotliwości na izolowanym uchwycie elektrody, gdy poziom bezpieczeństwa pracy urządzenia jest obniżony.
Maszyna przystosowana jest do pracy w cyklu automatycznym. Tryb automatyczny jest standardowym trybem pracy urządzenia podczas procesu produkcyjnego.
Zgrzewarka wysokiej częstotliwości umożliwia pracę w trybie ręcznym w celu regulacji.
Operatorzy maszyn powinni zawsze nosić standardową odzież roboczą i obuwie antypoślizgowe.
Środowisko pracy urządzenia, podłoga oraz ręczne uchwyty i uchwyty muszą być zawsze czyste i wolne od wszelkich zanieczyszczeń, smaru lub błota, aby zmniejszyć ryzyko poślizgnięcia się lub upadku do minimalnego możliwego poziomu.
Nigdy nie używać maszyny bez stałych lub ruchomych elementów ochronnych. Należy regularnie sprawdzać, czy wszystkie osłony i inne elementy ochronne są prawidłowo zamontowane i działają prawidłowo.
Bezpośredni kontakt z maszyną mogą mieć wyłącznie upoważnione osoby, które zostały odpowiednio przeszkolone w zakresie obsługi maszyny oraz bezpieczeństwa i higieny pracy.
Każdy operator urządzenia musi zostać poinstruowany w zakresie funkcji elementów zabezpieczających maszyny i ich prawidłowego użytkowania.
W obszarze otaczającym urządzenie (około 1,5 m wokół generatora i prasy) nie mogą znajdować się żadne przedmioty, które mogłyby zakłócać działanie urządzenia. Obszar ten musi być utrzymywany w czystości i odpowiednio oświetlony.
Proszę nigdy nie używać manipulatorów urządzenia lub elastycznych rur jako uchwytów. Proszę pamiętać, że każdy przypadkowy ruch manipulatora urządzenia może przypadkowo uruchomić proces spawania, zmienić parametry, a nawet spowodować awarię maszyny lub uszkodzenie jej narzędzi.
NALEŻY OBOWIĄZKOWO informować przełożonego i/lub personel ruchu drogowego o wszelkich przypadkach nieprawidłowego działania urządzenia.
Kategorycznie zabrania się zdejmowania osłon ochronnych podczas pracy urządzenia.
używanie WSZYSTKICH zaprojektowanych osłon i przycisków blokujących jest OBOWIĄZKOWE
Nigdy nie używać maszyny bez stałych lub ruchomych elementów ochronnych. Należy regularnie sprawdzać, czy wszystkie osłony i inne elementy ochronne są prawidłowo zamontowane i działają prawidłowo.
W obszarze otaczającym urządzenie (około 1,5 m wokół generatora i prasy) nie mogą znajdować się żadne przedmioty, które mogłyby zakłócać działanie urządzenia. Obszar ten musi być utrzymywany w czystości i odpowiednio oświetlony.
Środowisko pracy urządzenia, podłoga oraz ręczne uchwyty i uchwyty muszą być zawsze czyste i wolne od wszelkich zanieczyszczeń, smaru lub błota, aby zmniejszyć ryzyko poślizgnięcia się lub upadku do minimalnego możliwego poziomu.
6.3 Elementy sterujące i wskaźniki dostępne dla operatora
Wszystkie elementy sterujące i wskaźniki spawarki można łatwo znaleźć na jej konstrukcji lub na pulpicie sterowniczym. Przed przystąpieniem do pracy operator maszyny powinien zapoznać się z rozmieszczeniem elementów sterujących i wskaźników na maszynie, a także z funkcjami, którymi sterują.
Pełna lista wyżej wymienionych elementów sterujących i wskaźników dostępnych dla operatora znajduje się poniżej:
- PRZEŁĄCZNIK GŁÓWNY - przełącznik zainstalowany z przodu obudowy urządzenia, służy do włączania i wyłączania zasilania elektrycznego. Pozycja 1-ON oznacza, że przełącznik jest włączony, natomiast pozycja 0-OFF oznacza, że przełącznik jest wyłączony.
- POZIOM MOCY - Przełącznik jest zainstalowany z przodu obudowy urządzenia, stopniowa regulacja napięcia jest używana do regulacji napięcia anodowego Ua. Przełącza on gałęzie transformatora anodowego (Przełącznik krokowy od 0 do 1, 2 gdzie: 0 - oznacza, że transformator anodowy jest odłączony, 1 - oznacza, że poziom napięcia anodowego jest najniższy, 2 - oznacza, że poziom napięcia anodowego jest najwyższy).
- PANEL STEROWANIA HMI - panel PLC składający się z wyświetlacza ciekłokrystalicznego, na którym można znaleźć zaprogramowane parametry spawania oraz przycisków przełączających, które można wykorzystać w przypadku konieczności wyświetlenia parametrów.
- ZATRZYMANIE AWARYJNE - czerwony przycisk E-Stop z główką w kształcie grzybka, którego należy użyć do zatrzymania maszyny w razie awarii lub wypadku.
- USB - Port USB do przesyłania receptur i historii alarmów. Znajduje się na panelu operatora lub po prawej stronie urządzenia. Usługa archiwizacji danych została opisana w rozdziale 6.5. Port jest dodatkowym wyposażeniem maszyny.
- PRĄD AN ODOWY - amperomierz panelowy, który znajduje się na panelu sterowania (Rys. 8), powinien mierzyć prąd elektryczny w obwodzie anodowym i umożliwiać wizualną ocenę procesu spawania (charakterystyka obciążenia generatora).
- USTAWIENIE CIŚNIENIA - Ręcznie obsługiwany zawór redukcyjny (Rys. 8) jest zaworem służącym do ustawiania ciśnienia w układzie pneumatycznym maszyny (proszę pociągnąć zawór do góry i przekręcić: obrót w prawo - wyższe ciśnienie, obrót w lewo - niższe ciśnienie), znamionowe ciśnienie robocze maszyny wynosi 6 barów;
Poziom ciśnienia w układzie pneumatycznym nigdy nie przekracza poziomu ciśnienia napędzającego maszynę.
- WSKAŹNIK POŁOŻENIA D OLNEGO WYŁĄCZNIKA KRAŃCOWEGO - wycięcie w płytce z podziałką, umożliwiające obserwację położenia czerwonego wskaźnika, a tym samym obserwację położenia wysokości dolnego wyłącznika krańcowego, ułatwiając tym samym ustawienie go w dolnym położeniu.
- RESET - niebieski przycisk, który można znaleźć na stanowisku sterowania (Rys. 10), powinien być używany w przypadku, gdy maszyna musi zostać ponownie uruchomiona z powodu awarii lub powinna zostać włączona. Zdecydowanie zaleca się wdrożenie procedury ponownego testowania wszystkich systemów alarmowych za każdym razem, gdy maszyna jest włączona.
- STOP - czarny przycisk (Rys. 10) znajdujący się na stanowisku sterowania, należy użyć w celu zatrzymania procesu zgrzewania wysoką częstotliwością.
- START - Dwa zielone przyciski, które można znaleźć na stacji kontrolnej (Rys. 10), powinny być używane w celu uzyskania zgrzewu o wysokiej częstotliwości (oba przyciski należy nacisnąć jednocześnie).
- KOLUMNA ŚWIATEŁ SYGNALIZACYJNYCH
- A. Czerwony kolor wskazuje awarię i jednocześnie komunikat alarmowy powinien być wyświetlany na panelu dotykowym HMI.
Komunikaty alarmowe są kasowane, a czerwona lampka na kolumnie sygnalizacyjnej przestaje migać po naciśnięciu przycisku RESET. W przypadku, gdy wysiłki poszły na marne i komunikat alarmowy nie został usunięty po naciśnięciu przycisku RESET, może to oznaczać, że przyczyna wystąpienia awarii nie została jeszcze usunięta.
- Pomarańczowy kolor wskazuje, że spawarka wysokiej częstotliwości zaczyna działać.
- Zielony kolor oznacza, że urządzenie jest gotowe do pracy.
- A. Czerwony kolor wskazuje awarię i jednocześnie komunikat alarmowy powinien być wyświetlany na panelu dotykowym HMI.
- SYSTEM PRZYGOTOWANIA SPRĘŻONEGO POWIETRZA (Rys. 12) - składa się z:
- zacisk sprężonego powietrza, do którego należy podłączyć wąż sprężonego powietrza. Wąż powinien dostarczać do systemu sprężone powietrze o ciśnieniu od 4 do 8 barów
- ręcznie sterowany zawór odcinający sprężonego powietrza (w celu otwarcia zaworu należy przekręcić go w lewo i ustawić w pozycji ON; obrót w prawo - pozycja OFF - zawór jest zamknięty)
- ręczny zawór redukcyjny to zawór służący do ustawiania ciśnienia w układzie pneumatycznym maszyny (proszę pociągnąć zawór do góry i przekręcić: obrót w prawo - wyższe ciśnienie, obrót w lewo - niższe ciśnienie), znamionowe ciśnienie robocze maszyny wynosi 6 barów.
Poziom ciśnienia w układzie pneumatycznym nigdy nie przekracza poziomu ciśnienia napędzającego maszynę.
- filtr sprężonego powietrza wraz z mechanizmem uwalniania wody kondensacyjnej
- manometr wskazujący poziom ciśnienia w układzie sprężonego powietrza maszyny
- Ogranicznik docisku elektrody - przykręcany do tłoczyska siłownika służy do ograniczenia długości skoku siłownika i ma za zadanie zapobiegać "wyciskaniu" materiału spawalniczego spod elektrody.
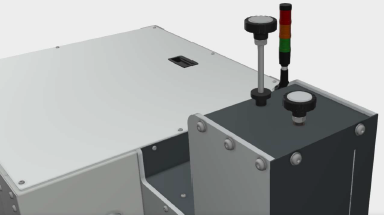
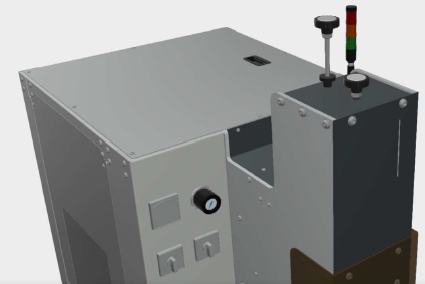
- ustawić materiał na stole roboczym - tak jak w przypadku spawania
- za pomocą dźwigni nożnej opuścić uchwyt z elektrodą na materiał (w taki sposób, aby elektroda tylko dotykała materiału, bez dodawania siły dociskającej) i pozostawić go
- Obracając pokrętło proszę przesunąć wyłącznik krańcowy w taki sposób, aby jego rolka znalazła się na wskaźniku wysokości elektrody. Dokręcić pokrętło
- podnieść uchwyt elektrody do górnego położenia za pomocą dźwigni nożnej
- opuścić uchwyt elektrody za pomocą dźwigni nożnej, docisnąć uchwyt elektrody do materiału i sprawdzić, czy rolka przełącznika zatrzymuje się na uchwycie elektrody.

Procedura odpowiedniej regulacji systemu kontroli wysokości:
- ustawić materiał na stole roboczym - tak jak w przypadku spawania
- za pomocą dźwigni nożnej opuścić uchwyt z elektrodą na materiał (w taki sposób, aby elektroda tylko dotykała materiału, bez dodawania siły dociskającej) i pozostawić go
- Obracając pokrętło (pokrętło oznaczone strzałką na Rys. 14) przesunąć wyłącznik krańcowy w taki sposób, aby jego rolka znalazła się na wskaźniku wysokości elektrody. Dokręcić pokrętło
- podnieść uchwyt elektrody do górnego położenia za pomocą dźwigni nożnej
- opuścić uchwyt elektrody za pomocą dźwigni nożnej, docisnąć uchwyt elektrody do materiału i sprawdzić, czy rolka przełącznika zatrzymuje się na wskaźniku wysokości elektrody i czy alert jest wyświetlany na panelu HMI w oknie głównym.

6.5 Programowanie i obsługa panelu dotykowego HMI
UWAGA! Każda wartość parametru przedstawiona na grafice niniejszej instrukcji jest losowa i nie powinna być brana pod uwagę przez operatora maszyny. Wartości parametrów powinny wynikać z praktycznego doświadczenia użytkownika, ponieważ mogą się one znacznie różnić w zależności od rodzaju spawanego materiału lub zastosowanego oprzyrządowania.
W panelu HMI wszystkie edytowalne wartości parametrów są wyświetlane na białym tle. Aby wyświetlić parametr, należy nacisnąć jego wartość, co spowoduje otwarcie klawiatury ekranowej. Dane można zapisać naciskając klawisz Enter.
6.5.1 Podłączenie do źródła zasilania
Krótko po podłączeniu urządzenia do źródła zasilania na wyświetlaczu HMI pojawi się okno alarmu wraz z następującym komunikatem:
#K001 PRZYCISK RESETOWANIA
W tej sytuacji maszyna musi zostać ponownie uruchomiona, więc należy nacisnąć niebieski przycisk RESET. Następnie musimy odczekać 30 sekund, aż maszyna będzie gotowa do pracy i przejdzie w tryb gotowości, co poznamy po następującej sekwencji zdarzeń: wskaźnik świetlny w kolumnie sygnału świetlnego miga na zielono, a niebieski pasek postępu na górnej krawędzi okna panelu HMI znika. Jeśli masaż alarmowy nie zniknie z wyświetlacza HMI, proszę zapoznać się z rozdziałem 6.5.2.
Do sprawdzić, czy wyświetlany jest sygnał alarmu
przycisk na górzeproszę nacisnąć pasek menu; jeśli nie ma żadnych komunikatów, grafika zmieni się na
6.5.2 Komunikaty alarmowe
Gdy wystąpi awaria maszyny lub gdy jeden z systemów zabezpieczających zostanie włączony lub gdy zostaną wykryte inne nieprawidłowości w funkcjonowaniu maszyny, na panelu dotykowym HMI zostanie wyświetlony jeden z komunikatów alarmowych. Wszystkie komunikaty alarmowe są usuwane za pomocą przycisku RESTART .

Rodzaje masaży alarmowych:
#K001 NACIŚNIJ PRZYCISK RESET -ten komunikat wskazuje, że ustała przyczyna co najmniej jednego z aktualnie wyświetlanych komunikatów alarmowych. Proszę nacisnąć niebieski przycisk RESET, aby przywrócić urządzenie do stanu gotowości.
#A001 ZATRZYMANIE AWARYJNE - jest wyświetlane, gdy:
- maszyna jest włączona - obwód bezpieczeństwa maszyny musi być zawsze sprawdzany po naciśnięciu przycisku RESET
- Czerwony grzybkowy przycisk ZATRZYMANIA AWARYJNEGO został naciśnięty i zablokował się. Należy go odblokować, obracając jego główkę w prawo.
#A002 TUBE TEMPERATURE (TEMPERATURA RURY ) - ten typ masażu oznacza, że albo nie ma chłodzenia rury wózka, albo wystąpiła awaria systemu chłodzenia i jest wyświetlany, gdy system ochrony termicznej rury jest uruchomiony, co oznacza, że rura wózka rozgrzała się do zbyt wysokiej temperatury i w rezultacie zawleczka taśmy rury, która była połączona z wyłącznikiem krańcowym za pomocą linki, została odlutowana.
Zawleczka jest przylutowana do opaski lampy za pomocą lutu o temperaturze topnienia znacznie niższej niż ta, przy której lampa się przegrzała (uległa uszkodzeniu). W przypadku nadmiernego wzrostu temperatury lampy zawleczka wypadnie z opaski, w wyniku czego zadziała wyłącznik krańcowy, jednocześnie wyświetlony zostanie komunikat alarmowy i odcięte zostanie zasilanie żarzenia w lampie. Wówczas należy usunąć przyczynę przegrzania.
UWAGA! Przewód nie powinien być mocowany do żadnych innych części urządzenia poza zawleczką opaski przykręconej do rury. Zlekceważenie powyższego ostrzeżenia może skutkować zablokowaniem wyłącznika krańcowego, co może doprowadzić do przegrzania rury jezdnej, a w konsekwencji do jej uszkodzenia.
If the cotter pin gets separated from the band, the band should be taken off from the tube, the pin should be soldered to the band with the standard solder used in electronic engineering (Melting point <190oC) so that the repaired part could be reattached to the tube.
Przegrzanie przewodu może być spowodowane przez:
- zanieczyszczenia znajdujące się w generatorze lub w chłodnicy rurowej
- awaria wentylatora chłodzącego rurkę lub awaria systemu zasilania wentylatora
- zablokowanie otworów wentylacyjnych maszyny lub nadmierna ilość ziemi zebrana przez filtry zainstalowane w otworach wentylacyjnych
- nadmierna temperatura otoczenia.
#A003 ANTIFLASH - ten rodzaj masażu oznacza, że zadziałał system ochrony przed zajarzeniem łuku podczas spawania - w związku z tym komunikatem proszę upewnić się, że ani podkładka izolacyjna, ani materiał spawany, ani elektroda spawalnicza nie zostały uszkodzone.
#A004 ANODE OVERLOAD - ten komunikat oznacza, że limit wzrostu anody został przekroczony, więc parametry mające zastosowanie do mocy uwalnianej podczas spawania muszą zostać dostosowane.
#A006 NISKIE CIŚNIENIE SPRĘŻONEGO POWIETRZA - komunikat ten oznacza, że w układzie pneumatycznym występuje brak ciśnienia powietrza lub poziom ciśnienia powietrza jest zbyt niski. Proszę upewnić się, że wąż dostarczający sprężone powietrze jest podłączony do maszyny lub poziom sprężonego powietrza jest odpowiedni, a następnie za pomocą regulatora zaworu redukcyjnego, który można znaleźć w układzie przygotowania sprężonego powietrza, wyregulować ciśnienie w maszynie do odpowiedniego poziomu.

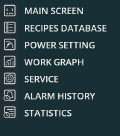





6.5.4 Ekran główny
Przepis - Pod tą nazwą można znaleźć grupę parametrów mających zastosowanie do cyklu pracy. Po ustaleniu parametrów spawania dla danego rodzaju produktu wynikających z praktycznego doświadczenia (wartości parametrów silnie zależą od wielkości spoiny, wielkości spawanego materiału i kształtu elektrody) należy je wprowadzić do systemu i zapisać pod nazwą receptury.
Dodatkowo, dwie wartości obok nazwy każdego parametru można również znaleźć na wyświetlaczu HMI. Pierwsza (na niebieskim tle) to wartość bieżącego parametru roboczego wyświetlana w czasie rzeczywistym, druga (na białym tle) to ustawiona wartość pochodząca z receptury produkcyjnej lub danych operatora.
W razie potrzeby operator może zawsze nacisnąć cyfrę na białym tle i zmienić jej wartość. Wartość bieżącego parametru roboczego zostanie natychmiast zaktualizowana, jednak zmiana nie ma wpływu na wykonywaną recepturę.
Aby zapisać zmiany w przepisie wprowadzone za pomocą ekranu głównego, proszę nacisnąć przycisk ZAPISZ PRZEPIS
aby skopiować parametry z ekranu głównego do paska Edytuj recepturę w oknie Baza danych receptur. Skopiowane parametry mogą zostać zapisane jako nowa receptura za pomocą przycisku Create new (Utwórz nową) lub mogą zostać użyte do aktualizacji istniejącej receptury za pomocą przycisku Update (Aktualizuj).
Nazwa: - nazwa receptury wykonywana na potrzeby produkcji.
Moc początkowa - parametr ten wskazuje pozycję (pojemność) kondensatora wyjściowego znajdującego się w generatorze; natężenie prądu anodowego w początkowej fazie spawania wysokiej częstotliwości silnie zależy od wartości tego parametru. (Parametr wyrażony w wartościach procentowych, gdzie 0% oznacza najniższy poziom pojemności - najniższy poziom natężenia prądu anodowego, a 100% oznacza najwyższy poziom pojemności - najwyższy poziom natężenia prądu anodowego).
-
Wartość parametru Moc początkowa i wartość prądu anodowego (moc uwalniana w materiale) nie są liniowo zależne, w związku z czym należy podjąć odpowiednie środki ostrożności podczas dostosowywania wartości tego parametru .
Bieżąca wartość parametru Initial power i wartość parametru Set są sobie równe tylko w początkowej fazie procedury spawania. Po rozpoczęciu procedury pozycja kondensatora wyjściowego jest automatycznie dostosowywana w celu osiągnięcia mocy roboczej.
Moc robocza - ten parametr określa prąd anodowy I używany do spawania. (Parametr wyrażony w amperach w zakresie od 0 do 4 A).
Wartości w kolorze zielonym na skali miernika prądu anodowego wskazują dopuszczalne wartości prądu anodowego Ia.
Po rozpoczęciu procedury spawania kondensator wyjściowy (moc początkowa) jest automatycznie regulowany w celu osiągnięcia mocy roboczej.
Czas opóźnienia - Ten parametr określa czas, w którym elektroda przylegała do spawanego materiału przed rozpoczęciem spawania. (Parametr wyrażony w sekundach w zakresie od 0 do 99 s).
Czas zgrzewania - ten parametr oznacza czas potrzebny urządzeniu do przetworzenia zgrzewu o wysokiej częstotliwości. (Parametr wyrażony w sekundach w zakresie od 0 do 99 s).
Czas stygnięcia - parametr ten określa czas, w którym elektroda była dociskana do spawanego materiału po zakończeniu spawania - materiał stygnie dociskany do stołu. (Parametr wyrażany w sekundach w zakresie od 0 do 99 s).
Tryb prądowy: 1 - Tryb zgrzewania typu prądowego oznacza, że licznik urządzenia rozpoczyna zliczanie czasu zgrzewania z wysoką częstotliwością, który został wprowadzony w parametrze Czas zgrzewania, gdy tylko urządzenie uzyska odpowiednią wartość prądu anodowego La, która powinna być albo większa, albo równa wartości wprowadzonej w parametrze Moc pracy. Mówiąc inaczej, w trybie zgrzewania prądowego czas zgrzewania jest równy sumie czasu potrzebnego na wytworzenie przez urządzenie prądu anodowego (wartość wprowadzona w parametrze Operating power) i czasu wprowadzonego w parametrze Welding time.
Jeśli urządzenie nie będzie w stanie osiągnąć mocy roboczej w ciągu 25 sekund, zacznie odliczać czas nagrzewania, a następnie zakończy cykl i wyświetli komunikat o nieosiągnięciu mocy roboczej.
0 - Tryb zgrzewania typu czasowego oznacza, że czas zgrzewania wysokiej częstotliwości jest równy wartości wprowadzonej w parametrze receptury pod nazwą Czas zgrzewania.
Warto zauważyć, że w trybie spawania typu czasowego cykl pracy może być wykonywany, nawet jeśli maszyna nie zdołała wytworzyć mocy roboczej, w wyniku czego uzyskana spoina może mieć nieregularną wytrzymałość.
Regulacja kondensatora:
1 - oznacza, że podczas spawania kondensator wyjściowy jest regulowany automatycznie, tak aby prąd anodowy był na poziomie ustawionym w parametrze Moc robocza.0 - sygnalizuje, że urządzenie pracuje w trybie ograniczonej automatycznej regulacji kondensatora wyjściowego. Podczas spawania kondensator wyjściowy jest regulowany tylko wtedy, gdy prąd anodowy przekracza wartość wprowadzoną w parametrze Power max.
Podczas pracy w trybie Regulacja kondensatora - 0 należy pamiętać, że jeśli moc początkowa będzie zbyt niska, urządzenie nie będzie w stanie automatycznie wyregulować prądu anodowego Ia w górę, aby osiągnąć wartość ustawioną w parametrze Prąd anodowy.
Korekcja mocy - parametr ten odnosi się do metody sterowania kondensatorem wyjściowym w fazie początkowej, gdy po włączeniu cyklu spawania kondensator dąży do uzyskania prądu roboczego. Parametr umożliwia wyłączenie regulacji kondensatora bez osiągnięcia ustawionego prądu roboczego.
- Przykład 1: Ustawiony prąd roboczy to 1A, pozycja startowa to 40%, regulacja kondensatora to 1, korekcja mocy to 0A.
- Po włączeniu cyklu spawania prąd roboczy wynosi 0,5 A.
- Rozpoczyna się regulacja kondensatora wyjściowego w celu osiągnięcia docelowego prądu roboczego 1A.
- Pozycja kondensatora zmienia się z 40% do 75% - Prąd roboczy osiąga wartość 1 A; regulacje kondensatora zatrzymują się.
- Cykl spawania jest kontynuowany.
- Przykład 2: Prąd roboczy jest ustawiony na 1 A; Pozycja początkowa jest ustawiona na 40%; Regulacja kondensatora jest ustawiona na 1; Korekta mocy jest ustawiona na -0,2 A.
- Po włączeniu cyklu spawania prąd roboczy osiąga poziom 0,5 A.
- Rozpoczyna się regulacja kondensatora wyjściowego w celu osiągnięcia docelowego prądu roboczego równego 1A, pomniejszonego o wartość korekcji mocy, która wynosi 1A - 0,2A = 0,8A.
- Pozycja kondensatora zmienia się z 40% na 60% - Prąd roboczy wynosi 0,8 A; regulacja kondensatora zostaje zatrzymana.
Parametr korekcji mocy jest stosowany w procesach spawania, w których w początkowej fazie prąd roboczy jest niski, po czym następuje bardzo dynamiczny wzrost prądu. Nałożenie się spontanicznego wzrostu prądu roboczego i regulacji kondensatora, powodującej jego wzrost, prowadzi do niedopuszczalnie wysokiej wartości prądu roboczego. Jeśli ustawienie kondensatora wyjściowego zostanie wyłączone przed osiągnięciem ustawionej wartości prądu roboczego, prąd może spontanicznie osiągnąć wymaganą wartość.
Większość procesów spawania nie wymaga stosowania korekcji mocy; parametr powinien być wtedy ustawiony na 0.
Parametry receptury - poziom mocy i ciśnienie z komentarzem wyświetlanym na żółto (USTAW RĘCZNIE) to tylko informacja dla operatora, który czytając parametry na ekranie dotykowym, musi ręcznie zmienić ustawienia z boku maszyny. Zmiana tego ustawienia na ekranie nie ma wpływu na ustawienia maszyny!
Poziom mocy - jest głównym ustawieniem mocy urządzenia; regulacja odbywa się poprzez zmianę napięcia anodowego Ua w zakresie od 1 do 2, gdzie 1 oznacza niską moc, a 2 maksymalną moc: 0 - transformator anodowy jest odłączony.
UWAGA! Proszę pamiętać, że pomimo tego, że wyżej wymienione parametry można zapisać pod nazwą receptury w panelu dotykowym HMI, istnieją również dwa inne parametry, takie jak: CIŚNIENIE i TEMPERATURA ELEKTRODY, które należy ustawić ręcznie.
Wartość napięcia anodowego Ua należy dobrać doświadczalnie w zależności od powierzchni spoiny i rodzaju materiału spawalniczego.
PRESSURE - - parametr wskazuje ciśnienie sprężonego powietrza w układzie pneumatycznym zacisku elektrody wyrażone w barach w zakresie od 0 do 6 bar; parametr określa siłę docisku elektrody w stosunku do materiału podczas spawania.
Poziom ciśnienia w układzie pneumatycznym, za pomocą którego elektroda jest dociskana do stołu, nigdy nie przekracza poziomu ciśnienia napędzającego maszynę.
Po ustawieniu poziomu mocy i ciśnienia na panelu HMI na ekranie głównym wyświetlone zostanie okno (Rys. 17) informujące operatora, że wartość tych parametrów należy ustawić ręcznie (za pomocą odpowiedniego przełącznika) i potwierdzić przyciskiem Zatwierdź.
Elektroda w dolnej pozycji alarmowej zostanie wyświetlone, gdy elektroda osiągnie dolną pozycję (ruch na czujniku).
Wykonane cykle: - oznacza licznik cykli zgrzewania wykonanych na urządzeniu. Jeśli operator przytrzyma przycisk Przycisk resetowania licznika
przez 3 sekundy, licznik zostanie zresetowany.
KOMUNIKATY ALARMOWE INFORMUJĄCE O BRAKU WARUNKÓW DO ROZPOCZĘCIA CYKLU SPAWANIA:
NOT READY (NIE GOTOWE ) - sygnalizuje, że urządzenie nie uruchomiło się ponownie prawidłowo i nie przeszło rozruchu trwającego kilka sekund. Proszę nacisnąć przycisk RESET na panelu sterowania. Stan rozruchu, czyli czas nagrzewania lampy, jest wyświetlany w postaci paska postępu w górnej części ekranu.
6.5.5 Baza danych przepisów
Baza danych przepisów.
Wszystkie receptury zapisane w pamięci panelu HMI są prezentowane w postaci kolumny RECIPE LIST. Parametry receptur zostały opisane w poprzednim rozdziale. Liczba receptur jest praktycznie nieograniczona. Zawartość receptury wyświetlana jest po prawej stronie, klikając na wartości na białym tle można zmienić wartości parametrów.
NOWY PRZEPIS: Aby utworzyć nową recepturę, proszę wypełnić wszystkie pola parametrów receptury, a następnie nacisnąć przycisk
. Nowy przepis pojawi się na liście przepisów.
W celu zapisania tych zmian w recepturze, które zostały wprowadzone przy użyciu funkcji Ekran głównyproszę nacisnąć przycisk PROSZĘ ZAPISAĆ PRZEPIS przycisk
aby skopiować parametry z ekranu głównego na ekran Proszę edytować przepis bar w Baza danych przepisów okno. Skopiowane parametry można zapisać jako nową recepturę za pomocą opcji Utworzyć nowy lub można ich użyć do aktualizacji istniejącej receptury za pomocą przycisku Aktualizacja przycisk.
Jeśli lista receptur zawiera już recepturę o takiej samej nazwie jak ta, która ma zostać zapisana, nie będzie możliwe zapisanie nowej receptury, a jedynie aktualizacja parametrów. W takim przypadku należy zmienić nazwę receptury.
WYDANIE Z PRZEPISAMI
Aby edytować przepis należy kliknąć na jego nazwę znajdującą się na liście przepisów (wybrany przepis powinien być podświetlony na żółto i wyświetlony w polu Proszę edytować przepis wiersz). Jeśli chodzi o zmianę wartości parametru w Proszę edytować przepis Jeśli chodzi o wiersz, musimy kliknąć białe pole, w którym powinien być wyświetlany, i wprowadzić nową wartość. Gdy procedura edycji zostanie zakończona, pojawi się okno Aktualizacja przycisk musi być wciśnięty
w wyniku czego wprowadzone zmiany we wskazanej recepturze zostaną zaakceptowane, zapisane i przechowywane.
Aby zapisać parametry przepisu z poziomu ekranu głównego, proszę nacisnąć przycisk ZAPISZ PRZEPIS
widoczne w tym oknie. Jeśli na liście receptur znajduje się receptura o tej samej nazwie, jej parametry zostaną zaktualizowane.
PROCEDURA USUWANIA
Aby wykonać procedurę usuwania receptury, proszę kliknąć na nazwę receptury znajdującą się na liście receptur (wybrana receptura powinna być podświetlona na żółto i wyświetlona w wierszu Edytuj recepturę ), a następnie nacisnąć przycisk Usuń.
PROCEDURA WYBORU RECEPTURY
Aby przeprowadzić procedurę wyboru receptury dla celów produkcyjnych, proszę wybrać z listy receptur recepturę z wartościami wymaganymi dla cyklu pracy (wybrana receptura powinna być podświetlona na żółto i wyświetlona w oknie dialogowym). Proszę edytować przepis wiersz), a następnie proszę kliknąć Załadunek do produkcji
w wyniku czego receptura zostanie przesłana do systemu i przygotowana do użycia w bieżącej produkcji, a jej parametry zostaną wyświetlone na ekranie. Ekran główny okno.
PROCEDURA SORTOWANIA
Receptury używane do produkcji są wymienione w kolejności alfabetycznej. Przy większej liczbie receptur, z boku tabeli pojawi się pasek przewijania, który pozwoli na płynne poruszanie się po tabeli. Możliwe jest również sortowanie receptur według nazwy, rosnąco lub malejąco. Aby posortować przepisy, proszę kliknąć na nagłówek listy - Lista przepisów; drugie naciśnięcie zmieni kierunek sortowania. Wszystkie dane są zapisywane w pamięci panelu HMI. W folderze "Recipe" znajdują się dwa pliki receptur: "Recipe.db" i "Recipe_a.rcp". Istnieje możliwość edycji receptur na komputerze. Możliwe jest skopiowanie plików receptur z pamięci panelu dotykowego na pamięć USB i edytowanie ich za pomocą bezpłatnego programu EasyBuider Pro. Pliki te mogą być używane jako kopia zapasowa receptur lub do przesyłania receptur do innego panelu dotykowego HMI.
6.5.6 Ustawienie mocy
Ustawienie mocy.
W oknie znajdują się dwa wskaźniki:
Prąd anodowy - wskaźnik natężenia prądu anodowego. Wskazuje natężenie prądu anodowego La, które powinno być równe natężeniu prądu miernika analogowego znajdującego się na panelu sterowania.
KONDENSATOR - narzędzie wskazujące pozycję kondensatora wyjściowego (w zakresie od 0 do 100%). Za pomocą tego narzędzia można ustawić odpowiedni poziom mocy - z reguły im większa pojemność, tym wyższy prąd anodowy La.
Grupa przycisków pod wskaźnikiem służy do regulacji kondensatora anodowego. Ustawienie można przeprowadzić na dwa sposoby:
AUTO - Przed rozpoczęciem spawania kondensator jest automatycznie ustawiany w pozycji odpowiadającej wartościom wprowadzonym w polu Moc początkowa parametr. Gdy procedura spawania jest wykonywana, pozycja kondensatora jest automatycznie dostosowywana tak, aby poziom natężenia prądu anodowego La mógł wzrosnąć do wartości zapisanej w parametrze. Moc operacyjna parametr.
Proszę wybrać tryb AUTO podczas standardowych cykli pracy wykonywanych przez urządzenie. Tryb MANUAL jest używany do procedur testowych.
RĘCZNY - cała procedura ustawiania kondensatora jest wykonywana ręcznie, w razie potrzeby operator może zmienić pozycję kondensatora za pomocą
lub
i jednocześnie regulowane jest natężenie prądu anodowego.
Power max. = Operating power + ... - parametr określa maksymalną wartość, o jaką można przekroczyć OPERATING POWER w celu uruchomienia automatycznego zmniejszania prądu anodowego z wykorzystaniem kondensatora wyjściowego (parametr określany w amperach, w zakresie 0 - 1A). Power min. = Operating power - ... - parametr określa minimalną wartość, o jaką może zostać przekroczona MOC EKSPLOATACYJNA w celu uruchomienia automatycznego zwiększania prądu anodowego z wykorzystaniem kondensatora wyjściowego (parametr określony w amperach, w zakresie 0 - 1A).
6.5.7 Wykres pracy
Wykres pracy.
Okno zawiera wykres przedstawiający szczegółowo działanie urządzenia. Możliwe jest obserwowanie zmian dwóch parametrów w czasie rzeczywistym:
- zmiany prądu anodowego (czerwona linia);
- zmiany położenia kondensatora wyjściowego (niebieska linia).
Wykres przedstawia dane zarejestrowane w przeszłości. W prawym górnym rogu znajduje się przycisk otwierający okno, w którym można wybrać okres, z którego dane mają być wyświetlane, oraz zmienić ustawienia wyświetlania wykresu.
6.5.8 Menu serwisowe
- Przykład 1: Ustawiony prąd roboczy to 1A, pozycja startowa to 40%, regulacja kondensatora to 1, korekcja mocy to 0A.
-
Menu serwisowe.
W tym oknie wyświetlane są następujące informacje pochodzenia statystycznego:
Liczba cyk li - jest to całkowita liczba cykli pracy od momentu pierwszego włączenia urządzenia.
Czas pracy - jest to całkowity czas pracy maszyny,
Antiflash - ta wartość wskazuje, ile razy od dnia wyprodukowania urządzenia system ochrony przed łukiem elektrycznym został włączony.
Alarm przeciążenia anody - wartość ta wskazuje, ile razy od dnia wyprodukowania urządzenia przekroczony został maksymalny poziom natężenia prądu w obwodzie anodowym i w rezultacie ile razy włączony został mechanizm zabezpieczający przed przeciążeniem anody.
Alarm przeciążenia sieci - wartość ta wskazuje, ile razy od dnia wyprodukowania urządzenia przekroczono maksymalny poziom natężenia prądu w obwodzie sieci podczas spawania, a w rezultacie ile razy włączono mechanizm ochrony przed przeciążeniem sieci.
Alarm temperatury rurki - ta wartość wskazuje, ile razy od dnia, w którym urządzenie zostało wyprodukowane, system ochrony termicznej rurki został automatycznie uruchomiony.
Parametry wymienione poniżej są dostępne tylko dla techników serwisowych producenta, dlatego do ich edycji wymagane jest hasło.
Kontrola procesu aktywna - aktywuje
lub dezaktywuje
ustawienia sterowania cyklem HF dla prądu roboczego (anodowego) podczas procesu spawania. Innymi słowy, wybranie przycisku powoduje, że podczas procesu spawania odnotowywany jest zakres tolerancji +/- prądu anodowego, określony w oknie serwisowym w parametrach sterowania procesem spawania. Parametry sterowania zostały opisane w dalszej części niniejszej instrukcji.
-
Power max = Operating power + - parametr ten określa maksymalną wartość natężenia prądu, która może przekroczyć wartość limitu Operating power w celu zainicjowania automatycznej procedury obniżania prądu anodowego wykonywanej przez kondensator wyjściowy (parametr wyrażony w amperach w zakresie od 0 do 1A).
Moc min = Moc robocza - . .. - Ten parametr jest używany tylko do sterowania procesem spawania i do określania dolnego zakresu tolerancji prądu.
-
Czas opóźnienia dociśnięcia - wartość ta wskazuje czas, który upływa od momentu wyzwolenia dolnego wyłącznika krańcowego (wskazującego dolne położenie elektrody) do momentu dociśnięcia elektrody do materiału z pełną siłą.
Ustaw % spawania w tolerancji: - ten parametr określa procentową wartość czasu, przez który prąd musi mieścić się w tolerancji. Gdy określony próg procentowy nie zostanie osiągnięty, na panelu HMI zostanie wyświetlony alarm wskazujący, że parametry spawania nie zostały osiągnięte: #A013 PARAMETRY SPAWANIA NIE ZOSTAŁY OSIĄGNIĘTE. W statystykach, kolumna Cycle Status (Status cyklu) będzie wskazywać 0 dla aktualnie wykonywanego cyklu.
Całkowity czas spawania [s]: - ten parametr pokazuje całkowity czas ostatniego spawania.
Czas spawania w tolerancji [s]: - Ten parametr pokazuje czas ostatniego spawania; jest on jednak liczony tylko dla prądu mieszczącego się w zakresie tolerancji +/- (Moc maks./min) określonym w powyższych parametrach.
-
Procent zgrzewania w tolerancji [%] - Ten parametr pokazuje procent czasu, w którym prąd mieścił się w zakresie tolerancji +/- podczas całego cyklu, który został ostatnio przeprowadzony na urządzeniu. W przypadku alarmu można szybko zdiagnozować, jaki procent czasu zgrzewania został osiągnięty dla wyżej wymienionych parametrów.
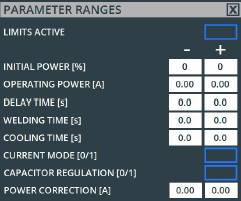



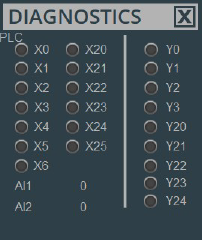


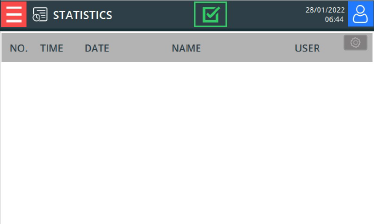
Time - czas wykonania zapisu
Moc robocza [A] - wartość parametru wykorzystywanego w procesie
Regulacja kondensatora [0 /1] - wartość parametru wykorzystywanego w procesie
- parametr Current Mode był ustawiony na 0 - średnia jest liczona od momentu włączenia wysokiej częstotliwości
- parametr Current Mode jest ustawiony na 1 - średnia jest liczona od momentu uzyskania ustawionej wartości prądu roboczego;
Licznik cykli - wartość pokazywana na liczniku cykli od pierwszego uruchomienia urządzenia.
LOGOWANIE OPERATORA
Panel dotykowy można zabezpieczyć przed nieautoryzowanym dostępem. Aby włączyć lub wyłączyć funkcję logowania użytkownika, należy przejść do okna serwisowego, a następnie kliknąć obszar zaznaczony poniżej na czerwono:
Otworzy się następujące okno:
Aktywne logowanie - przycisk aktywuje lub
dezaktywuje proces logowania. Aby przełączać się między funkcjami, należy wprowadzić hasło 21369.
Poniżej wymieniono komunikaty wyświetlane na urządzeniu w zależności od tego, czy użytkownik loguje się, dodaje nowego użytkownika, usuwa użytkownika, zmienia uprawnienia użytkownika lub zmienia hasło.
- Sukces! (może pojawić się podczas logowania, dodawania nowych użytkowników, usuwania użytkowników, zmiany uprawnień użytkownika, zmiany hasła).
- Nieprawidłowe hasło! (może pojawić się tylko podczas logowania).
- Konto już istnieje! (może pojawić się tylko podczas dodawania użytkownika).
- Niedopuszczalne znaki w haśle! (może pojawić się podczas dodawania użytkownika i zmiany hasła).
- Niedopuszczalne znaki w nazwie! (może pojawić się tylko podczas dodawania użytkownika)
1.Po włączeniu urządzenia proszę kliknąć na przycisk "Log-in" w oknie panelu dotykowego.
2. Otworzy się kontekstowe okno logowania.
3. Proszę wybrać odpowiedniego użytkownika z listy rozwijanej.
4. Proszę wprowadzić odpowiednie hasło, a następnie potwierdzić je przyciskiem Enter na klawiaturze.
5. Proszę nacisnąć przycisk Log-in.
6. Na ekranie pojawi się odpowiedni komunikat.
Po wyłączeniu urządzenia użytkownik jest automatycznie wylogowywany.
TWORZENIE NOWYCH UŻYTKOWNIKÓW
1. Proszę zalogować się jako użytkownik posiadający uprawnienia do zarządzania użytkownikami.
2. Proszę wybrać ikonę
3. Proszę wprowadzić nazwę użytkownika w polu użytkownika (litery i cyfry)
4. Proszę wprowadzić hasło w polu hasła (litery i cyfry)
5. Proszę wybrać poziom uprawnień, które powinien posiadać tworzony użytkownik.
A - podstawowe prace na maszynie
B - nieprzypisane
C - edycja receptury
D - nieprzypisane
E - nieprzypisane
F - parametry usługi, zarządzanie użytkownikami
6. Proszę wybrać przycisk Dodaj.
7. Na ekranie pojawi się odpowiedni komunikat.
USUWANIE UŻYTKOWNIKÓW
1. Proszę zalogować się jako użytkownik posiadający uprawnienia do zarządzania użytkownikami.
2. Proszę wybrać ikonę
3. Proszę wybrać odpowiedniego użytkownika z listy rozwijanej.
4. Proszę nacisnąć przycisk usuwania.
5. Na ekranie pojawi się odpowiedni komunikat.
ZMIANA UPRAWNIEŃ PRZYPISANYCH DO UŻYTKOWNIKA.
1. Proszę zalogować się jako użytkownik posiadający uprawnienia do zarządzania użytkownikami.
2. Proszę wybrać ikonę
3. Proszę wybrać odpowiedniego użytkownika z listy rozwijanej
4. Proszę wybrać lub usunąć wybór poziomu autoryzacji dla danego użytkownika.
5. Proszę nacisnąć przycisk Zmień.
6. Na ekranie pojawi się odpowiedni komunikat.
ZMIANA HASŁA
1. Proszę się zalogować. Operator może zmienić tylko swoje własne hasło; jednak przełożony może zmienić hasło dowolnego użytkownika
2. Proszę wybrać ikonę
3. Proszę wybrać odpowiedniego użytkownika z listy rozwijanej (jeśli są Państwo zalogowani jako administratorzy).
4. Proszę wprowadzić nowe hasło
5. Proszę nacisnąć przycisk Zmień.
6. Na ekranie pojawi się odpowiedni komunikat.
FABRYCZNIE UTWORZONYCH UŻYTKOWNIKÓW I PRZYPISANYCH IM HASEŁ
NAZWA UŻYTKOWNIKA - HASŁO
OPERATOR - 33
SUPERVISOR - 11
Miller Weldmaster - PRZEZNACZONE DO SERWISU PRODUCENTA;
Uprawnienia:
OPERATOR - praca na maszynie, możliwość wyboru i edycji receptur.
SUPERVISOR - praca na maszynie, wybór receptury, edycja receptur, zmiana parametrów, dodawanie i usuwanie operatorów oraz zmiana haseł innych użytkowników.
Dane zarchiwizowane w pamięci panelu dotykowego HMI

Poniższe oprogramowanie jest wymagane do odczytu i konwersji plików historii i receptur na komputerze z systemem operacyjnym Windows:
- bezpłatne oprogramowanie EasyBuider Pro, które można pobrać z panelu HMI ze strony producenta: http://www.weintek.com/ lub przedstawiciela w Polsce http://www.multiprojekt.pl/ftp/weintek_hmi/easy_builder_pro/
- Microsoft Excel lub inny program do obsługi arkuszy kalkulacyjnych.
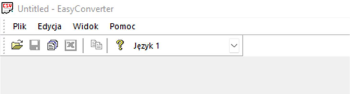
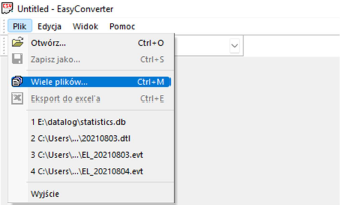
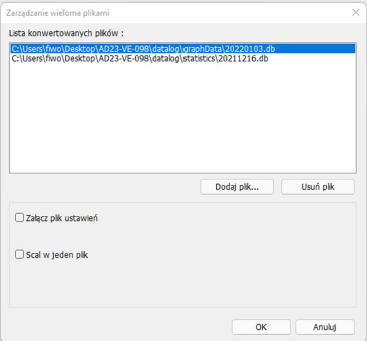
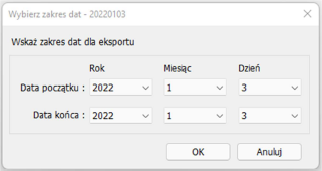
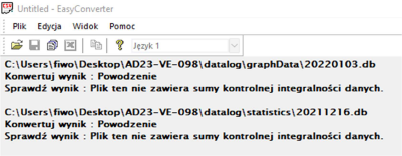
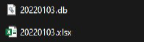
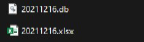
- Na komputerze wyposażonym w bezprzewodową kartę sieciową proszę wybrać sieć o nazwie odpowiadającej numerowi fabrycznemu urządzenia zapisanemu na jego tabliczce znamionowej, na przykład: D120-XM-003.
- Proszę wprowadzić hasło odpowiadające numerowi fabrycznemu urządzenia dużymi literami, zaczynając od końca, bez myślników, na przykład: 300MX021D.
- Proszę przejść do okna usługi, a następnie kliknąć obszar zaznaczony poniżej na czerwono.
- Otworzy się okno z ustawieniami zaawansowanymi, w którym można znaleźć adres IP panelu HMI i aktualnie załadowany projekt.
KOPIOWANIE PLIKÓW HISTORII Z PANELU HMI PRZY UŻYCIU SIECI WI-FI
- Proszę otworzyć Eksplorator Windows w dowolnym folderze i wpisać następującą formułę w pasku adresu, gdzie znajduje się adres IP, na przykład: 192.168.1.50; należy wpisać adres odczytany z panelu dotykowego: ftp://uploadhis:753456@192.168.1.50/
- Następnie proszę kliknąć "Enter
- Otworzy się okno zawierające pamięć panelu dotykowego
- Struktura folderu została opisana w jednym z kolejnych rozdziałów. Można skopiować całą zawartość każdego folderu. Możliwe jest również kopiowanie pojedynczych plików przechowywanych w folderach.
DANE ZARCHIWIZOWANE W PAMIĘCI PANELU DOTYKOWEGO HMI
- Proszę włożyć urządzenie pamięci USB do portu panelu dotykowego HMI.
- Na ekranie panelu HMI pojawi się okno, w którym należy nacisnąć przycisk Upload przed zakończeniem odliczania.
- W następnym oknie proszę wybrać dane do pobrania, wprowadzić hasło:
- 753456, proszę wybrać lokalizację /usbdisk/disk_a_1 i nacisnąć przycisk Upload, aby rozpocząć pobieranie plików.
STRUKTURA PLIKÓW HISTORII I RECEPTUR
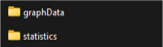
- ""recipe" - w folderze "recipe" znajdują się trzy pliki: "recipe.db" "recipe_a.rcp" oraz "recipe.rcp". Plik "recipe.db" zawiera receptury zapisane w panelu HMI. Może on służyć jako kopia zapasowa lub do przesyłania receptur do innego panelu dotykowego HMI. Receptury można również edytować na komputerze.
- "datalog" - w folderze "datalog" znajduje się folder "graphData" i folder "statistics".
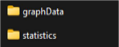
- "graphData" - w folderze "GraphData" znajdują się pliki zawierające zapisy parametrów pracy urządzenia. Każdego dnia pracy urządzenia zapisywany jest jeden plik z nazwą daty. Zapisywane są również następujące dane:
- C [%] - pozycja kondensatora
- Ia [A] - natężenie prądu anodowego
Wszystkie te parametry są zapisywane raz na 0,5 sekundy i tylko podczas cyklu. Są one zapisywane w tabeli.
- "statistics" - w folderze "statistics" znajdują się pliki z zapisami statystyk procesu. Każdego dnia pracy urządzenia zapisywany jest jeden plik z nazwą daty. Zapisywane są również następujące dane:
- nazwa receptury - nazwa receptury użytej do wykonania zarejestrowanego cyklu roboczego.
- user - nazwa operatora zalogowanego podczas cyklu.
- capa position [%] - wstępnie ustawiona pozycja początkowa kondensatora.
- prąd [A] - ustawiony prąd roboczy.
- delay time [s] - ustawiony czas opóźnienia.
- Czas zgrzewania [s] - ustawiony czas nagrzewania.
- cool time [s] - ustawiony czas chłodzenia.
- power level - ustawiony poziom mocy.
- ciśnienie [bar] - ustawione ciśnienie.
- bieżący tryb - wartość zadana bieżącego trybu .
- regulacja kondensatora - wartość zadana regulacji kondensatora.
- bieżąca korekta - wartość parametru używanego w procesie.
- kontrola procesu - informacje o aktywnej kontroli procesu.
- status procesu - status kontroli procesu, gdzie -1 oznacza nieaktywną kontrolę procesu,
- oznacza błąd - proces przerwany lub parametry spawania nie zostały osiągnięte, 1 oznacza sukces - proces spawania przebiegł zgodnie z parametrami ustawionymi dla prądu.
- current status - status bieżącego sterowania, gdzie -1 oznacza nieaktywne sterowanie procesem,
- oznacza błąd - proces przerwany lub parametry spawania nie zostały osiągnięte, 1 oznacza sukces - proces spawania przebiegł zgodnie z ustawionymi parametrami.
- prąd średni - średnia wartość prądu podczas spawania.
- licznik - licznik cykli maszyny.
- eventlog"- w folderze "eventlog" znajdują się pliki z zapisem historii komunikatów alarmowych, które zostały wyświetlone podczas pracy urządzenia. Historia komunikatów alarmowych jest przechowywana w pliku o nazwie EL_data, na przykład: EL_20220105. Zapisywane są również następujące informacje:
- Zdarzenie - informacja, gdzie 0 wskazuje, kiedy wystąpił komunikat alarmowy, a 2 wskazuje, kiedy komunikat alarmowy został zresetowany.
- Kategoria - nieistotne
- Komunikat - treść komunikatu alarmowego
- Proszę podłączyć pamięć USB ze zgranymi recepturami do komputera i otworzyć program Utility Manager.
- W lewym górnym rogu okna proszę kliknąć Select screen i wybrać model panelu: cmt X Serie - Basic.
- W zakładce Data Conversion proszę wybrać aplikację Recipe Database Editor.
- W aplikacji Recipe Database Editor proszę kliknąć na Import... i wybrać pliki ze skopiowanymi recepturami "recipe.db".
- Otworzy się okno edycji przepisu.
- Po zakończeniu edycji proszę kliknąć Eksportuj... i zapisać plik w poprzedniej lokalizacji.
KOPIOWANIE PRZEPISÓW Z PAMIĘCI USB:
- 1. Proszę włożyć pamięć USB z zapisanymi recepturami do gniazda panelu dotykowego HMI. Plik receptury musi znajdować się w folderze "recipe" dokładnie tak, jak podczas pobierania receptur z panelu
- Na ekranie panelu HMI pojawi się okno, proszę kliknąć Pobierz.
- W kolejnym oknie proszę wybrać Recipe database; wybrać lokalizację pliku receptury; wprowadzić hasło: 753456 i kliknąć przycisk Download.
Przepisy zostaną załadowane do pamięci panelu dotykowego HMI. Proszę wyłączyć, a następnie włączyć urządzenie.
6.6 Podłączenie do źródła zasilania
POD ŻADNYM POZOREM maszyna nie może być obsługiwana przez niewykwalifikowany personel. Operatorzy maszyny muszą być zaznajomieni z zasadami bezpieczeństwa i higieny pracy.
Przed podłączeniem urządzenia do źródła zasilania należy wykonać następujące procedury:
- upewnić się, że środowisko pracy maszyny (maszyna i jej otoczenie) jest czyste i uporządkowane lub nie ma żadnych przeszkód, które mogłyby negatywnie wpłynąć na standardowy cykl pracy maszyny; oraz
- upewnić się, że przygotowano odpowiednią ilość surowca (próbki testowe); oraz
- upewnić się, że pojemniki na odpady i pojemniki na produkty spawane są ustawione w odpowiednim miejscu, ale w pobliżu maszyny, zgodnie z wymaganiami Bayer dotyczącymi cyklu produkcyjnego, jeśli takie istnieją; oraz
- Elektroda spawalnicza powinna być zamontowana na zacisku (wyjątek stanowi sytuacja, gdy elektroda jest umieszczona na materiale, a następnie dociśnięta zaciskiem).
- upewnić się, że wszystkie osłony są odpowiednio przymocowane do maszyny, a boczne drzwi skrzynki rozdzielczej są zamknięte;






- Podnieść elektrodę do górnego położenia.
- Proszę przekręcić przełącznik MAIN SWITCH do pozycji 0-OFF - oznacza to, że urządzenie jest wyłączone.
- Zakręcić ręcznie sterowany zawór odcinający sprężonego powietrza (w celu wykonania procedury - przekręcić zawór w prawo - pozycja OFF).
- Proszę uporządkować środowisko pracy wokół maszyny.
- Zarówno wtyczka zasilania elektrycznego, jak i wtyczka układu sprężonego powietrza powinny być odłączone w przypadku dłuższej przerwy w pracy (obie wtyczki należy wyciągnąć z gniazdek).
REGULACJA RÓWNOLEGŁOŚCI STOŁU
W przypadku korekty równoległości między powierzchnią spawania elektrody a powierzchnią stołu roboczego zaleca się regulację położenia elektrody za pomocą śrub regulacyjnych.
REGULACJA DŹWIGNI NOŻNEJ
Ruch do przodu lub do tyłu dźwigni nożnej można regulować za pomocą nakrętek, z których jedna jest oznaczona literą A na Rys. 32. Druga nakrętka znajduje się po przeciwnej stronie. Po obu stronach dźwigni nożnej wywiercone są również otwory umożliwiające jej opuszczenie w razie potrzeby.
6.7 Procedura testowania i ustawiania


Procedura testowania i ustawiania powinna być stosowana w praktyce, gdy:
- urządzenie zostało włączone po raz pierwszy,
- konieczna jest wymiana oprzyrządowania (gdy zajdzie taka potrzeba),
- procedura konserwacji została zakończona,
- operatorzy muszą być zaznajomieni z funkcjonalnością maszyny.
Aby wykonać wspomnianą procedurę, operator powinien:
1. Proszę upewnić się, że przełącznik Ua SETTING, który znajduje się z boku urządzenia, jest ustawiony w pozycji 0 - OFF.2. Ułożyć materiał przeznaczony do spawania na stole roboczym

3. Proszę docisnąć dźwignię nożną i zacisk z elektrodą do materiału.

7. Proszę kilkakrotnie podnieść i opuścić zacisk z elektrodą, aby upewnić się, że porusza się on płynnie i czy elektroda jest równoległa do stołu.





- MOC POCZĄTKOWA
- MOC OPERACYJNA
- CZAS OPÓŹNIENIA
- CZAS SPAWANIA
- CZAS CHŁODZENIA.
Gdy testom poddawany jest nowy rodzaj materiału, zdecydowanie zaleca się wprowadzenie do systemu parametrów cykli spawania o niskich wartościach, a następnie stopniowe zwiększanie ich wartości aż do uzyskania najbardziej pożądanego efektu spawania.
14. Za pomocą ręcznie obsługiwanego zaworu redukcyjnego ciśnienia (rys. 8 - cyfra 7) ustawić poziom docisku elektrody używanej w procesie spawania.
15. Proszę nacisnąć na panelu HMI: HMI → Ekran główny → Bieżący tryb → 0 lub 1
16. Proszę nacisnąć na panelu HMI: HMI → Ekran główny → Regulacja kondensatora →.
Tryb prądu 0/1 i regulacja kondensatora 0/1 zostały szczegółowo opisane w rozdziale 6.5.4.
17. Proszę ustawić wartość korekcji mocy, jeśli jest potrzebna. Ten parametr został opisany w rozdziale 6.5.4.
18. Proszę upewnić się, że podkładka izolacyjna na stole roboczym lub na rozdzielaczu z blachy aluminiowej jest czysta - nie może być zabrudzona ani uszkodzona mechanicznie w miejscu, w którym elektroda jest dociskana do spawanego materiału.
UWAGA! Podkładkę izolacyjną należy umieścić bezpośrednio pod spawanym materiałem, ponieważ ma ona chronić operatora przed łukiem elektrycznym powstającym między elektrodą spawalniczą a stołem roboczym.
UWAGA! Jeśli rozdzielacz został pokryty podkładką izolacyjną, powinien ściśle przylegać do stołu - w taki sposób, aby między rozdzielaczem a stołem roboczym nie było żadnych zanieczyszczeń.
Uwaga! Proszę unikać umieszczania czegokolwiek pod elektrodą masową. Jeśli podczas procesu spawania wymagane jest umieszczenie spawanego materiału pod elektrodą masową, warstwa pod elektrodą masową powinna być jak najcieńsza.
19. Proszę opuścić zacisk z elektrodą za pomocą dźwigni nożnej. Proszę zaobserwować, czy komunikat pojawi się w głównym oknie panelu HMI informując, że elektroda osiągnęła dolną pozycję.
20. Nacisnąć jednocześnie oba przyciski START, gdy elektroda jest dociśnięta do materiału. Przytrzymać wciśnięte przyciski START do momentu odliczenia parametrów spawania ustawionych w recepturze. Zwolnienie przycisków podczas cyklu spowoduje jego zatrzymanie.
UWAGA: Aby włączyć zgrzew wysokiej częstotliwości, należy jednocześnie nacisnąć oba przyciski START na stacjach sterujących. Do wykonania tej operacji należy użyć obu rąk. W trybie ręcznym należy nacisnąć i nie puszczać przycisków przez cały czas zgrzewania. Wszelkie inne czynności podejmowane w celu pominięcia naciśnięcia przycisków obiema rękami są surowo zabronione.
UWAGA: proces spawania w urządzeniu jest sygnalizowany na kolumnie lampki sygnalizacyjnej (pomarańczowa lampka).
UWAGA: Podczas spawania zbliżanie się do uchwytu, elektrody lub falowodu, a tym bardziej dotykanie ich częściami ciała lub metalowymi przedmiotami jest surowo zabronione ze względu na ryzyko poparzenia elektrycznego, zapalenia łuku elektrycznego lub zanieczyszczenia narzędzi.
UWAGA: przycisk ZATRZYMANIA AWARYJNEGO jest przeznaczony do naciśnięcia w dowolnym momencie, zwłaszcza gdy konieczne jest natychmiastowe wyłączenie awaryjne.
21. Proszę obserwować wskazania amperomierza. PRĄD ANODOWY - prąd płyty powinien wzrastać w zakresie zielonego obszaru wskazanego w tabeli amperomierza.
22. Proszę użyć dźwigni nożnej, aby podciągnąć elektrodę i sprawdzić jakość spoiny.
23. Sprawdzić gładkość spoiny.
24. W zależności od wyniku pierwszego zgrzewu (zgrzany, niezgrzany, przegrzany) odpowiednio dostosować parametry zgrzewania:
- MOC POCZĄTKOWA
- MOC OPERACYJNA
- CZAS OPÓŹNIENIA
- CZAS SPAWANIA
- CZAS CHŁODZENIA
- CIŚNIENIE (wyregulować ręcznie)
- POZIOM MOCY (wyregulować ręcznie)
- TRYB BIEŻĄCY
- REGULACJA KONDENSATORA
- KOREKTA MOCY.
25. Maszyna powinna przejść wiele godzin testów. Powinna być testowana, gdy produkt jest powtarzalny. Zdecydowanie zaleca się sprawdzenie cyklu pracy maszyny, jej funkcjonalności i ergonomii na linii produkcyjnej.
26. Po uzyskaniu zadowalającego wyniku spawania pod względem wytrzymałości i estetyki wizualnej proszę zapisać parametry spawania jako recepturę: HMI → Ekran główny → przycisk Zapisz recepturę → Okno bazy danych receptur → proszę wpisać nową nazwę receptury w kolumnie NAZWA → proszę wybrać przycisk
. Nowy przepis pojawi się na liście przepisów.
6.9 Cykl pracy i obowiązki operatora

1. Uruchomić urządzenie zgodnie z procedurą opisaną w rozdziale 6.7.



- Moc początkowa;
- Moc robocza;
- Czas opóźnienia;
- Czas spawania;
- Czas chłodzenia
- Poziom mocy




UWAGA: , Proces HF można zatrzymać w dowolnym momencie za pomocą przycisku STOP na stacji sterującej.
UWAGA: Aby włączyć zgrzewarkę HF, należy jednocześnie nacisnąć oba przyciski START na stacjach sterujących. Do wykonania tej operacji należy użyć obu rąk. W trybie automatycznym nie jest konieczne przytrzymywanie przycisków przez cały czas trwania cyklu. W cyklu automatycznym przyciski służą wyłącznie do rozpoczęcia procesu spawania. Wszelkie inne czynności podejmowane w celu pominięcia wciskania przycisków obiema rękami są surowo zabronione.
UWAGA: proces spawania w urządzeniu jest sygnalizowany na kolumnie lampki sygnalizacyjnej (pomarańczowa lampka).
UWAGA: Podczas spawania dotykanie uchwytu, elektrody, falowodu częściami ciała lub metalowymi przedmiotami jest surowo zabronione ze względu na ryzyko poparzenia elektrycznego, zapalenia łuku elektrycznego lub zniszczenia narzędzia.

Poza mocą wyjściową, siłą docisku i równoległym położeniem elektrod, inne istotne znaczenie dla procesu zgrzewania ma rodzaj materiału bazowego rozprowadzonego na uziemionym wałku pod folią. Należy unikać spawania bez warstwy materiału podstawowego - stosowanie materiału podstawowego zmniejsza ryzyko porażenia prądem. Materiał bazowy powinien mieć niski współczynnik strat dielektrycznych. Mogą to być na przykład płyty epoksydowo-szklane, politetrafluoroetylen (teflon), poliester (MYLAR), płyty Presspan, Resotex, bakelit itp. Grubość i twardość materiału bazowego zależy od grubości zgrzewanej folii. Zazwyczaj cieńszy materiał bazowy powinien być stosowany do grubszych folii, a grubszy materiał bazowy - do cieńszych folii. Grubość materiału bazowego może wynosić od 0,1 do 1,5 [mm] i powinna być dobrana do danego rodzaju folii i warunków spawania w trakcie kilku eksperymentów.
UWAGA: Należy unikać spawania bez podkładu. Zastosowanie odpowiedniego podkładu zmniejsza liczbę przepięć na elektrodzie.
7.2. WYBÓR MOCY POCZĄTKOWEJ
W celu osiągnięcia najwyższej możliwej wydajności i małej liczby odrzutów, należy dostosować moc dla każdej elektrody za pomocą przełącznika POWER LEVEL. Pierwszy element umożliwia regulację mocy zasilania generatora, natomiast drugi - regulację mocy dostarczanej do elektrody i emitowanej do spawanego materiału. Regulację mocy należy przeprowadzić w trakcie kilku eksperymentów (zgodnie z instrukcją podaną przez producenta).
Po zwiększeniu mocy wyjściowej należy obserwować amperomierz mierzący prąd anodowy. Jego wzrost oznacza rozpoczęcie procesu spawania.
Czas spawania należy ustawić na taką wartość, aby wysoka częstotliwość została wyłączona, gdy wskazówka amperomierza zatrzyma się. Sprawdzić jakość spawania. Jeśli jakość jest niewystarczająca, należy zwiększyć moc wyjściową, a jeśli to nie pomoże, wydłużyć czas zgrzewania. Nie należy ustawiać zbyt wysokiej mocy wyjściowej - może to doprowadzić do uszkodzenia produktów, a nawet materiału podstawowego i elektrod.
Należy przyjąć jako zasadę, że w przypadku zgrzewania twardego PVC, czas zgrzewania nie powinien przekraczać 4 - 5 sekund. Eksperymenty wykazały, że dłuższy czas zgrzewania, wykraczający poza ww. zakres, praktycznie nie ma wpływu na jakość zgrzewania, natomiast znacząco obniża wydajność procesu. Jeśli przeprowadzone przez Państwa eksperymenty wykażą, że operacja spawania trwa dłużej niż 8 sekund, świadczy to jedynie o niewłaściwym doborze generatora do obciążenia lub zainstalowaniu elektrody o zbyt dużej powierzchni. Po odłączeniu napięcia od elektrod, zgrzewane materiały powinny ostygnąć pod prasą. Jeśli elektroda zostanie podniesiona zbyt wcześnie, gdy materiał nadal nadaje się do formowania, materiał spawany jest niewłaściwie chłodzony i ulega deformacji. Pozytywny wpływ elektrody na proces chłodzenia jest łatwy do zrozumienia, jeśli zdadzą sobie Państwo sprawę, że chociaż elektroda wydaje się być bardzo ciepła, jej temperatura jest nadal znacznie niższa niż temperatura zgrzewanej folii. W rezultacie elektroda może pochłaniać ciepło ze spawanej warstwy i szybko ją schładzać.
W związku z tym konieczne jest pozostawienie spawanego materiału do ostygnięcia pod jednostką prasującą przez 0,52 sekundy. Czas chłodzenia należy dobrać w trakcie kilku eksperymentów, pamiętając, że zbyt długi czas chłodzenia oznacza niepotrzebne straty czasu produkcji
Zgrzewanie miękkiej folii PVC wymaga docisku elektrod do zgrzewanego materiału. Pomiar optymalnego docisku elektrod może być trudny i w praktyce nie jest konieczny. W celu dobrania odpowiedniego docisku, zwykle wystarczy rozpoznać przypadki nieprawidłowego zgrzewania i wygląd nieprawidłowego zgrzewania, które mogą wskazywać na niewłaściwe dobranie docisku. Na zbyt niskie ciśnienie mogą wskazywać następujące objawy:
- podatność na wyładowania iskrowe występujące między dwiema elektrodami, ponieważ powietrze, które powinno zostać wyciśnięte, występuje między dwiema warstwami folii, w wyniku czego powstaje nieregularne natężenie prądu;
- występowanie pęcherzyków powietrza w szwie;
- pojawienie się wytrzymałości szwu, która jest niewielka
Jeśli ciśnienie jest szczególnie niskie, może wystąpić coś, co zwykle nazywa się "wrzeniem folii". Gdy folia jest zgrzewana pod bardzo niskim ciśnieniem, może zostać zdeformowana w spieniony produkt o bardzo niskiej rezystancji. Stosowanie nadmiernego ciśnienia jest również niewłaściwe, ponieważ może spowodować, że folia będzie bardzo cienka wzdłuż miejsca zgrzewania, a tym samym spowoduje niższą rezystancję zgrzewanego materiału. Dlatego też zaleca się przestrzeganie zasady mówiącej, że grubość folii po zgrzaniu powinna być równa co najmniej połowie początkowej grubości obu warstw folii. Istotny wpływ na właściwości rezystancyjne zgrzewanego materiału ma również pojawienie się i odpowiedni kształt charakterystycznej nieszczelności, która zazwyczaj tworzy się wzdłuż obu krawędzi zgrzewanego miejsca. Jeśli taki wyciek się nie pojawia, świadczy to zazwyczaj o niewystarczającej rezystancji zgrzewanego miejsca, co można bardzo łatwo sprawdzić. Brak wycieku po procesie spawania może być spowodowany zastosowaniem zbyt niskiej mocy wyjściowej lub niewystarczającego ciśnienia. Jeśli używają Państwo elektrod z krawędziami tnącymi, bardzo ważne jest prawidłowe ustawienie krawędzi tnącej. Zazwyczaj przyjmuje się, że krawędź tnąca elektrody powinna wystawać z płaszczyzny zgrzewania o około połowę grubości zgrzewanej warstwy. W celu sprawdzenia działania krawędzi tnącej należy wykonać kilka próbnych cykli zgrzewania i usunąć skrawki folii. Wynik testów można uznać za zadowalający, gdy usunięcie skrawków folii wzdłuż linii zgrzewania zajmuje nie więcej niż jedno cięcie nożyczkami .
8.0 Konserwacja
Dzięki zastosowanym rozwiązaniom konstrukcyjnym i nieskomplikowanej budowie maszyny, zarówno konserwacja prewencyjna, jak i awaryjna oraz czynności kontrolne są stosunkowo proste i nie wymagają długich przerw w pracy maszyny.
Spawarka wymaga niewielkiego nakładu pracy związanego z obsługą i konserwacją urządzenia, pod warunkiem zachowania odpowiednich warunków użytkowania. Konieczne jest regularne sprawdzanie stanu technicznego podłączenia maszyny do sieci zasilającej, w szczególności stanu układu ochrony przeciwporażeniowej.
Wszystkie elementy generatora wysokiej częstotliwości, w szczególności wszystkie elementy izolacyjne, muszą być utrzymywane w czystości. Należy dokładnie czyścić wnętrze układu wyjściowego generatora co najmniej raz na trzy miesiące. Po takim czyszczeniu należy sprawdzić stan komponentów generatora i jednostek bezpośrednio współpracujących z generatorem oraz dokręcić wszystkie połączenia.
Ze względu na specyficzne właściwości urządzenia zaleca się, aby niektóre z wyżej wymienionych czynności były wykonywane przez autoryzowany i odpowiednio wykwalifikowany personel serwisu technicznego Producenta (dotyczy to w szczególności sytuacji awaryjnych). Wyżej wymienione czynności wymagają szczególnej ostrożności i uwagi.
UWAGA: Podczas pracy generatora, jego komponenty, a także komponenty obwodu wyjściowego, mają napięcie do 8 kV DC i napięcie o wysokiej częstotliwości do 220 V (27,12 MHz).
UWAGA: Kondensatory generatora anodowego mogą utrzymywać ładunek elektryczny o napięciu do 8000 VDC nawet po odłączeniu spawarki od źródła zasilania. Przed dotknięciem elementów generatora wysokiej częstotliwości kondensatory te należy zawsze rozładować.
Uziemienie konstrukcji maszyny należy wykonać ze szczególną ostrożnością. Proszę pamiętać, że generator nigdy nie może pracować, gdy osłony ochronne są zdjęte, również podczas serwisu technicznego i czynności konserwacyjnych, gdy poziom bezpieczeństwa maszyny może być niższy z powodu wykonywanej naprawy.
Wszelkie prace konserwacyjne i naprawy wymagają zezwolenia upoważnionych osób.
Powinni Państwo przechowywać REJESTR MASZYNw tym daty i rodzaje wykonanych czynności zapobiegawczych lub napraw.
Podczas wykonywania zadań konserwacyjnych lub innych wymaganych czynności manualnych nigdy nie należy wchodzić ani wkładać żadnych części ciała do obszaru narażonego na potencjalne i przewidywalne zagrożenia, aby wyeliminować ryzyko potencjalnych i przewidywalnych sytuacji niebezpiecznych.
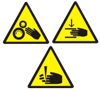
Należy zawsze nosić odzież ochronną i obuwie antypoślizgowe, co zmniejsza ryzyko upadku. Należy zawsze upewnić się, że rękawy są dobrze zaciśnięte wokół nadgarstków lub odpowiednio podwinięte.
Podczas pracy z elementami o ostrych krawędziach należy zawsze używać rękawic roboczych.
Cały personel odpowiedzialny za obsługę i konserwację maszyny powinien zostać odpowiednio przeszkolony i poinstruowany.
Każda czynność konserwacyjna lub naprawcza może być wykonywana wyłącznie przez autoryzowany i wykwalifikowany personel, zdolny do prawidłowej interpretacji usterek i awarii, czytania schematów instalacji i rysunków technicznych, w celu zapewnienia, że wszystkie czynności demontażu i montażu związane ze standardowymi procedurami konserwacyjnymi są wykonywane w sposób profesjonalny i - co najważniejsze - bezpieczny.
Wszystkie czynności wykonywane w zakresie obsługi zespołu prasującego, tj. montaż i demontaż elektrody, wykonywane przy włączonym zasilaniu maszyny, mogą być wykonywane wyłącznie przez personel odpowiednio przeszkolony w zakresie BHP, w tym w szczególności w zakresie ryzyka związanego z obsługą zespołu prasującego.
Należy również przewidzieć potencjalne niestandardowe zachowanie maszyny w przypadku rozszczelnienia układu pneumatycznego zgrzewarki lub przewodów doprowadzających sprężone powietrze. Spowoduje to powolne automatyczne opuszczanie zespołu dociskowego zgrzewarki.
Personel powinien zostać poinformowany o takim ryzyku podczas szkolenia w zakresie bezpieczeństwa i higieny pracy.
UWAGA: Podczas każdej z wyżej wymienionych czynności maszyna musi być zatrzymana.
8.2 Program zapobiegawczy - kontrole okresowe
NA POCZĄTKU KAŻDEJ ZMIANY
- Sprawdzić, czy obszar roboczy maszyny jest czysty i uporządkowany;
- Proszę sprawdzić wzrokowo, czy ekrany ochronne są zablokowane;
- Sprawdzić oświetlenie obszaru roboczego;
- Proszę sprawdzić, czy przycisk ZATRZYMANIA AWARYJNEGO działa prawidłowo;
- Proszę sprawdzić główne zabezpieczenie w instalacji elektrycznej;
- Sprawdzić stan miedzianych i mosiężnych elementów przewodzących w obszarze uchwytu elektrody i elementów uziemiających bocznych ekranów ochronnych.
CO 100 GODZIN PRACY MASZYNY (CO NAJMNIEJ RAZ W TYGODNIU):
- Sprawdzić, czy śruby nośne (w tym w szczególności śruby mocujące narzędzia) są prawidłowo zamocowane i dokręcone;
- Sprawdzić poziom wody kondensacyjnej w zbiorniku filtra sprężonego powietrza; jeśli jest woda, opróżnić zbiornik; jeśli są duże ilości zanieczyszczeń stałych, zdemontować i umyć zbiornik;
CO 500 GODZIN PRACY MASZYNY (ALE NIE RZADZIEJ NIŻ CO DWA TYGODNIE)
- Sprawdzić, czy radiator lampy anodowej jest czysty;
- Sprawdzić ilość zanieczyszczeń stałych i pyłu w komorze generatora; w razie potrzeby oczyścić komorę za pomocą odkurzacza lub pistoletu na sprężone powietrze;
- Sprawdzić, czy elementy ruchome (w szczególności narzędzia i prowadnice) są czyste;
- Nasmarować elementy ruchome - w szczególności prowadnice; jeśli to konieczne, należy użyć stałego smaru na bazie litu i smarownicy;
- Sprawdzić i przetestować jednostkę alarmową.
CO 1000 GODZIN PRACY MASZYNY (ALE NIE RZADZIEJ NIŻ CO SZEŚĆ MIESIĘCY)
- Sprawdzić wzrokowo stan elementów mechanicznych;
- Dokręcić wszystkie śruby;
- Proszę sprawdzić, czy środki ochrony przed porażeniem prądem działają prawidłowo;
- Sprawdzić skuteczność smarowania prowadnic;
- Sprawdzić stan głównych elementów stykowych - należy wymienić główne styczniki lub inne elementy stykowe systemu, takie jak styczniki lub przekaźniki o nadmiernie zużytych powierzchniach.
UWAGA: Przed każdą konserwacją należy wyłączyć urządzenie za pomocą WYŁĄCZNIKA GŁÓWNEGO i odłączyć zasilanie sieciowe.
UWAGA: Przed każdą konserwacją należy wyłączyć urządzenie za pomocą WYŁĄCZNIKA GŁÓWNEGO i odłączyć zasilanie sieciowe.
Najważniejszymi elementami zastosowanymi w maszynie, służącymi do podniesienia i zapewnienia bezpieczeństwa jej pracy są:
- czujniki z otwartą obudową
- łatwo dostępny wyłącznik awaryjny umieszczony na kasecie sterowniczej, który wyłącza maszynę w dowolnym momencie
- zestaw czujników i detektorów sprawdzających poprawność działania maszyny i jej poszczególnych układów, połączonych z sygnalizacją na panelu operatora
- dodatkowe zabezpieczenia w algorytmie sterowania maszyną, które zapobiegają uruchomieniu maszyny w potencjalnie niebezpiecznych sytuacjach
- sama konstrukcja maszyny zapewnia maksymalne bezpieczeństwo jej działania.
9.1 Podstawowe wymagania
Kwestie związane z bezpieczeństwem i higieną pracy oraz oceną ryzyka podczas kontaktu człowieka z maszyną zostały szczegółowo opisane w poprzednich rozdziałach niniejszej instrukcji. Ponieważ kwestia ta jest niezwykle istotna, niektóre instrukcje zostały powtórzone w niniejszym rozdziale.- Urządzenie może być używane wyłącznie w sposób odpowiedni do jego przeznaczenia wyraźnie opisanego w punkcie 1.
- Zastosowane rozwiązania konstrukcyjne związane z bezpieczeństwem ograniczają do minimum zarówno niestandardowe zachowania maszyny, jak i zagrożenia dla operatorów i innych osób mających kontakt z maszyną, pod warunkiem przestrzegania zasad bezpiecznej pracy. Maszyna wyposażona jest w wyłączniki klawiszowe na osłonach zabezpieczających oraz przycisk ZATRZYMANIA AWARYJNEGO.
- Każdy nowy pracownik mający kontakt ze spawarką powinien zostać przeszkolony w zakresie podstawowych zasad bezpieczeństwa i higieny pracy oraz zapoznany z rodzajami zagrożeń związanych z obsługą spawarki, o ile operator nie przestrzega obowiązujących przepisów i zasad.
- Personel odpowiedzialny za obsługę spawarki musi posiadać gruntowną wiedzę z zakresu udzielania pierwszej pomocy w przypadku porażenia prądem elektrycznym i oparzeń. W przypadku osób pracujących z urządzeniami wykorzystującymi fale elektromagnetyczne o częstotliwości w zakresie 0,1 - 300 MHz wymagane są okresowe badania lekarskie.
- Po zainstalowaniu spawarki należy zmierzyć emisję pola elektromagnetycznego i wyznaczyć granice strefy niebezpiecznej.
- UWAGA: lampa zawiera metale ziem rzadkich i tlenki metali ziem rzadkich, które są wysoce toksyczne. W przypadku stłuczenia, lampę należy zutylizować z najwyższą ostrożnością i przy pomocy wyspecjalizowanych służb
- Na podstawie wyników pomiarów, zgodnie z obowiązującymi normami, określany jest poziom zagrożenia i czas, przez jaki operatorzy mogą przebywać w strefie niebezpiecznej.
- Do strefy niebezpiecznej mogą wejść wyłącznie operatorzy, którzy posiadają odpowiednie uprawnienia do pracy w obszarze narażonym na działanie pola elektromagnetycznego na podstawie specjalistycznych badań lekarskich oraz zostali odpowiednio przeszkoleni w zakresie bezpiecznej obsługi urządzeń emitujących pole elektromagnetyczne.
- Powyższe pomiary powinny być wykonywane przez autoryzowaną instytucję. Szczegółowe instrukcje dotyczące takich pomiarów są określone przez obowiązujące przepisy w kraju, w którym maszyna jest używana.
- Odbiorca urządzenia ponosi pełną odpowiedzialność prawną i finansową za wszelkie zdarzenia wynikające z nieznajomości niniejszej dokumentacji lub nieprzestrzegania zasad bezpieczeństwa. Przeczytanie i przestrzeganie ich oznaczeń jest ABSOLUTNIE OBOWIĄZKOWE
- Na podstawie informacji zawartych w niniejszej dokumentacji oraz znajomości własnej technologii produktu, Odbiorca zobowiązany jest do opracowania INSTRUKCJI OBSŁUGI dla pracowników obsługujących niniejszą maszynę.
- Przed rozpoczęciem jakiejkolwiek pracy na maszynie, każdy operator musi zapoznać się z treścią niniejszej dokumentacji i mieć przygotowaną INSTRUKCJĘ OBSŁUGI.
- Operatorzy maszyn powinni zawsze nosić standardową odzież roboczą, rękawice, nakrycia głowy i obuwie antypoślizgowe.
- Środowisko pracy maszyny, podłoga oraz ręczne uchwyty i uchwyty muszą być zawsze czyste i wolne od wszelkich zanieczyszczeń, smaru lub błota, aby zmniejszyć ryzyko poślizgnięcia się lub upadku do minimalnego możliwego poziomu.
- Nigdy nie używać maszyny w trybie automatycznym bez stałych lub ruchomych elementów zabezpieczających. Należy regularnie sprawdzać, czy wszystkie wyłączniki awaryjne i inne elementy zabezpieczające są prawidłowo zamontowane i działają prawidłowo.
- Każdy operator maszyny musi zostać poinstruowany o funkcjach elementów ochronnych maszyny i ich prawidłowym użytkowaniu.
- W obszarze otaczającym urządzenie (około 1,5 m wokół urządzenia) nie mogą znajdować się żadne przedmioty, które mogłyby zakłócać działanie urządzenia. Obszar ten musi być utrzymywany w czystości i odpowiednio oświetlony.
- Proszę nigdy nie używać manipulatorów maszyny lub przewodów elastycznych jako uchwytów. Proszę pamiętać, że każdy przypadkowy ruch manipulatora maszyny może przypadkowo uruchomić działanie maszyny.
- Proszę zawsze informować przełożonego i/lub personel drogowy o wszelkich przypadkach nieprawidłowej obsługi maszyny.
- Wszelkie prace konserwacyjne i naprawy wymagają zezwolenia upoważnionych osób.
- Powinni Państwo prowadzić Rejestr maszynyw tym daty i rodzaje wykonanych czynności zapobiegawczych lub napraw.
- Podczas wykonywania zadań konserwacyjnych lub innych wymaganych czynności manualnych nigdy nie należy wchodzić ani wkładać żadnych części ciała do obszaru narażonego na potencjalne i przewidywalne zagrożenia, aby wyeliminować ryzyko potencjalnych i przewidywalnych sytuacji niebezpiecznych.
PROSZĘ NIGDY NIE UŻYWAĆ SPAWARKI, GDY OSŁONY OCHRONNE SĄ ZDJĘTE LUB GDY PRZEŁĄCZNIKI KLUCZOWE SĄ ZABLOKOWANE. DOTYCZY TO W SZCZEGÓLNOŚCI EKRANÓW OCHRONNYCH GENERATORA. Osłony te zmniejszają emisję pola elektromagnetycznego i zapobiegają przypadkowemu dotknięciu elementów obwodu elektrycznego o napięciu zasilania lub wysokim napięciu do 8000 V.
- Należy zawsze nosić odzież ochronną i obuwie antypoślizgowe, co zmniejsza ryzyko upadku. Należy zawsze upewnić się, że rękawy są dobrze zaciśnięte wokół nadgarstków lub odpowiednio podwinięte.
- Podczas pracy z gorącymi komponentami lub komponentami o ostrych krawędziach należy zawsze używać rękawic roboczych.
- Należy również pamiętać, że na elementach, które ze względów ergonomicznych nie zostały osłonięte żadną osłoną, tj. na elektrodzie i przewodzących elementach uchwytu elektrody, występuje napięcie o wysokiej częstotliwości. PROSZĘ NIGDY NIE DOTYKAĆ TYCH ELEMENTÓW PODCZAS PROCESU SPAWANIA.
- Dotknięcie tych elementów podczas procesu spawania skutkuje poparzeniem skóry napięciem o wysokiej częstotliwości. Nie jest to jednak niebezpieczne dla życia lub zdrowia.
- Przyjęty sposób zasilania zgrzewarki stwarza potencjalne zagrożenie przygniecenia lub zmiażdżenia kończyn w przestrzeni pomiędzy dociskami elektrod. Wszelkie prace w obszarze działania zespołu dociskowego, tj. montaż i demontaż elektrod czy rozsypywanie i usuwanie materiału i złomu, które są wykonywane przy podłączonym zasilaniu zgrzewarki, mogą być wykonywane wyłącznie przez pracowników przeszkolonych w zakresie BHP, w tym w zakresie informacji o zagrożeniu stwarzanym przez zespół dociskowy.
- Podczas pracy maszyny operator powinien znajdować się w obszarze pokazanym poniżej
Obszar roboczy ZD-NX-4 (kolor zielony)
9.3 Warunki bezpieczeństwa pracy personelu odpowiedzialnego za konserwację i naprawy spawarki- Wszelkie prace konserwacyjne i naprawy wymagają zezwolenia upoważnionych osób.
- ZABRANIA SIĘ wykonywania jakichkolwiek prac serwisowych, konserwacyjnych lub zapobiegawczych bez odłączenia urządzenia od zasilania. Prace te wymagają szczególnej ostrożności. Należy zawsze pamiętać, że kondensatory generatora anodowego mogą utrzymywać ładunek elektryczny o napięciu 5000 V nawet po odłączeniu zgrzewarki od sieci zasilającej. Przed dotknięciem elementów generatora wysokiej częstotliwości, kondensatory te muszą być zawsze rozładowane.
- Zabrania się smarowania urządzenia podczas pracy.
- Cały personel odpowiedzialny za obsługę i konserwację maszyny powinien zostać odpowiednio przeszkolony i poinstruowany.
- Podczas pracy generatora, jego komponenty, a także komponenty obwodu wyjściowego, mają napięcie o wysokiej częstotliwości. Uziemienie konstrukcji maszyny musi być wykonane ze szczególną starannością. Należy również pamiętać, że czas pracy generatora ze zdjętymi osłonami należy ograniczyć do minimum.
- Wszelkie naprawy muszą być wykonywane zgodnie z obowiązującymi zasadami naprawy i eksploatacji urządzeń przez osobę posiadającą odpowiednie uprawnienia wydane przez właściwe Stowarzyszenie Elektryków (w Polsce: SEP).
- Każda czynność konserwacyjna lub naprawcza może być wykonywana wyłącznie przez autoryzowany i wykwalifikowany personel, zdolny do prawidłowej interpretacji usterek i awarii oraz czytania schematów instalacji, aby zapewnić, że wszystkie czynności demontażu i montażu związane ze standardowymi procedurami konserwacyjnymi są wykonywane w sposób profesjonalny i - co najważniejsze - bezpieczny.
- Podczas wykonywania zadań konserwacyjnych lub innych wymaganych czynności manualnych nigdy nie należy wchodzić ani wkładać żadnych części ciała do obszaru narażonego na potencjalne i przewidywalne zagrożenia, aby wyeliminować ryzyko potencjalnych i przewidywalnych sytuacji niebezpiecznych.
- korzystanie z urządzenia w sposób inny niż opisany w niniejszej instrukcji obsługi i konserwacji
- nieprawidłowa instalacja, wykonana niezgodnie z procedurami opisanymi w niniejszej instrukcji
- niewłaściwa obsługa urządzenia lub obsługa przez personel bez odpowiedniego przeszkolenia
- dostarczanie przez maszynę niewłaściwych parametrów
- niewystarczająca konserwacja urządzenia
- nieautoryzowanych zmian lub ingerencji osób nieposiadających wymaganych licencji, zezwoleń lub przeszkolenia,
- używanie części zamiennych innych niż oryginalne
- wszelkie działania osób niezgodne z zasadami określonymi w niniejszej instrukcji obsługi i konserwacji oraz wszelkie ostrzeżenia.
10.0 Dokumentacja elektryczna
10.1 Parametry zasilacza - dane techniczne
Zasilanie |
3 x 220 VAC; 50/60 Hz |
Ochrona głowy |
40 A |
Moc zainstalowana |
6 kVA |
Moc wyjściowa HF |
4 kW |
Napięcie robocze |
24 VDC |
Częstotliwość pracy |
27,12 MHz |
Stabilność częstotliwości |
+/- 0.6 % |
Lampa generatora (trioda metalowo-ceramiczna) |
7T85RB |
System obwodu zapobiegającego rozładowaniu |
kompletny ANTIFLASH z filtrem HF |
10.2 Lista urządzeń elektrycznych
Wszystkie podzespoły zastosowane w urządzeniu są typowymi podzespołami elektrycznymi dostępnymi w każdym specjalistycznym sklepie. Producent dobierając te elementy, w przypadku ich wymiany, pozostawia wybór odbiorcy, pod warunkiem, że zastosowane zamienniki będą posiadały takie same parametry techniczne. Wykaz urządzeń elektrycznych zawiera rozdział 13.3. W razie jakichkolwiek pytań prosimy kontaktować się z producentem.
10. 3 Rysunki koncepcyjne instalacji elektrycznej
UWAGA: Schemat okablowania znajduje się w załączniku do niniejszej instrukcji.
Proszę zobaczyć załącznik
11.0 Dokumentacja pneumatyczna
11.1 Dane techniczne
Ciśnienie robocze |
0,4 - 0,8 MPa |
Zużycie sprężonego powietrza |
Maks. 11 nl (standardowo) na cykl |
Czystość powietrza |
zgodnie z normą ISO8573-1:4-4-4 |
Wydajność filtrowania |
20 um (ISO8573-1 4-4-4) |
System pneumatyczny spawarki działa prawidłowo:
- jednostka prasowa

PROSZĘ ZOBACZYĆ DODATKI
12.0 Instrukcje ogólne
12.1 Instrukcje ogólne
Zastosowane rozwiązania konstrukcyjne oraz wysokiej jakości komponenty pozwalają na prawidłową eksploatację maszyny przez okres około 30 lat. Mogą jednak nastąpić zmiany w potrzebach Użytkownika Końcowego lub zmiany w zasadach lub normach, których nie można dziś przewidzieć, co może wymagać utylizacji maszyny przed upływem ww. okresu. Dotyczy to również wymienianych lub naprawianych części lub podzespołów zgrzewarki.
Użytkownik końcowy jest zobowiązany do zapewnienia, że utylizacja maszyny lub jej komponentów odbywa się zgodnie z obowiązującymi wymogami prawnymi obowiązującymi w danym momencie i w danym miejscu.
Wszystkie elementy maszyny nadają się do recyklingu. Utylizacja odpadów niebezpiecznych musi być zawsze przeprowadzana przez wyspecjalizowane firmy.
Rodzaje odpadów wytwarzanych podczas cyklu życia maszyny opisano poniżej w punkcie 12.2.
12.2 Odpady
Wszystkie odpady powstałe w trakcie wymiany lub serwisu technicznego, które są zanieczyszczone smarem, nie mogą być usuwane razem z odpadami przemysłowymi.- płynne lub stałe odpady tłuszczu
- smar pozostały po smarowaniu lub konserwacji maszyny
- kawałki szmatki lub papieru nasączone substancjami używanymi do czyszczenia elementów urządzenia
- używane części zamienne maszyny, w zależności od materiału, z którego są wykonane
- lampa generatora!!!
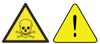
Wszystkie odpady powstałe w trakcie wymiany lub serwisu technicznego, które są zanieczyszczone smarem, nie mogą być usuwane razem z odpadami przemysłowymi. Wszystkie odpady powstające w procesie produkcji powinny być segregowane i składowane w wyznaczonych i oznakowanych miejscach.

12. 3 Procedura demontażu urządzenia przed utylizacją
-
- Ustawić maszynę tak, aby stała nieruchomo.
- Odłączyć zasilanie urządzenia.
- Odłączyć dopływ sprężonego powietrza do urządzenia.
- Proszę usunąć elastyczne przewody plastikowe lub gumowe i zlecić ich utylizację wyspecjalizowanej firmie.
- Odłączyć i usunąć przewody i urządzenia elektryczne oraz zapewnić ich utylizację przez wyspecjalizowaną firmę.
- Proszę posegregować elementy stalowe i elementy wykonane z metali nieżelaznych i zapewnić ich utylizację przez wyspecjalizowaną firmę.
13.0 Załączniki
13.1 Znacznik modelu i numeru seryjnego
Każda maszyna Miller Weldmaster posiada naklejkę umieszczoną z tyłu maszyny. Identyfikuje ona model i numer seryjny każdej spawarki.
Podane zostanie również napięcie i częstotliwość wymagana do pracy.
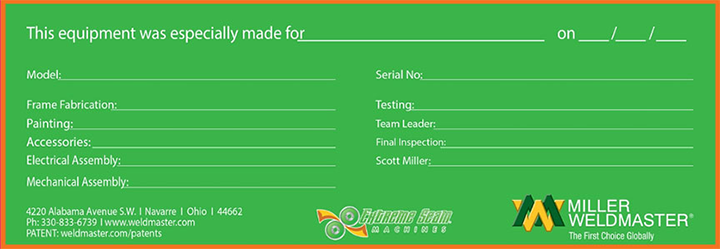